Performance Comparison of Axial Flux and Radial Flux Permanent Magnet Synchronous Motor
Radial flux permanent magnet synchronous (RFPM) motor has been widely used in electric vehicles and other applications in recent years because of its relatively mature design technology, high efficiency and smooth operation. In order to study the feasibility and rationality of AFPM motor design for range extender, the electromagnetic performance of AFPM and RFPM synchronous motor is compared and analyzed in this paper. Firstly, the flux paths of two kinds of motors with different topologies are summarized. Secondly, the finite element method is used to optimize the design of the motor. Finally, the electromagnetic performance of the motor under no-load and load conditions is compared and analyzed, which can provide some reference for the design of range extender generator.
1 Axial flux and radial flux permanent magnet motor
Although both AFPM and RFPM motors belong to permanent magnet synchronous motors, there are great differences in motor structure, flux path direction and stator manufacturing.
1.1 Motor structure
Figure 1 shows the model of AFPM and RFPM motors, and the main components of the two motors are composed of the stator part (stator core and winding) and the rotor part (permanent magnet and rotor core). The stator core of AFPM motor
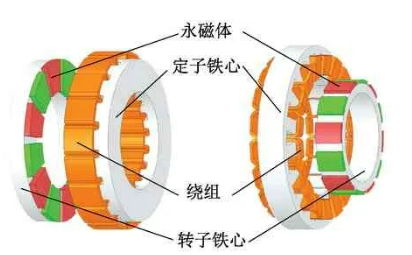
1.2 Magnetic flux path direction
The flux path of AFPM motor and RFPM motor is shown in Figure 2 and Figure 3, and the dashed line in the figure is a closed loop of the flux path generated by a pair of N and S poles. The flux paths of the two topological structures are basically the same, which are issued by the N-pole permanent magnet, through the air gap, stator part, air gap, S-pole, rotor core, and finally back to the N-pole circuit. But the direction of flux path is different between the two topologies. The whole flux path of AFPM motor is closed first in axial direction, then in circumferential direction through stator yoke, then in axial direction to S-pole, and finally in circumferential direction through rotor disk. The flux path direction of the RFPM motor is first radial, then circumferential closure by the stator yoke, then radial closure to the S pole, and finally circumferential closure by the rotor core to form the whole circuit.
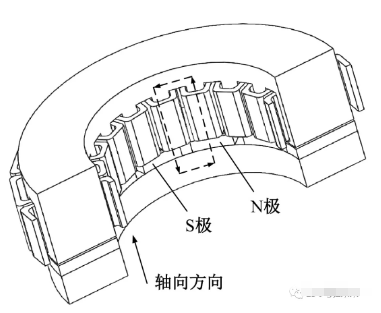
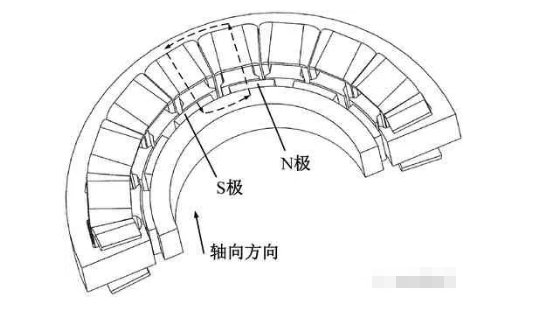
The flux path direction of the AFPM motor is parallel to the axis direction and closed along the axis and circumferential direction, while the flux path of the RFPM motor is perpendicular to the axis direction and closed along the radial and circumferential direction. The internal space of the AFPM motor is larger, which is more conducive to the heat dissipation of the motor. Generally, in order to further reduce the loss of stator winding and the amount of copper used in the end, fractional slot concentrated winding is usually used, which can improve the efficiency and reduce the cost of the motor to a certain extent.
1.3 Stator ManufacturingFor RFPM motor, in order to reduce the loss of stator core, usually with slotted silicon steel sheet axial press into the stator core, the winding wound on the stator teeth, the use of slot wedges to seal the slot to prevent winding off.
The AFPM motor stator manufacturing methods are various, there are two more common manufacturing methods: the use of automatic winder to wind the stator made; The stator tooth, the stator yoke and the winding are spliced together.Fig.4 shows the winding stator core model. However, when the winding is wound by the structure, the winding temperature is higher because of the small space at the inner diameter of the motor, the installation of the winding is difficult, and the electric load at the inner diameter is larger. FIG. 5 is a spliced stator core diagram. First, the winding is wound on the stator tooth part, and then the plurality of stator teeth are spliced with the stator yoke formed by superposition pressure to form the stator part. The advantage of this structure is that it can reduce the length of the winding end and reduce the harmonic of the induction electromotive force. But the stator teeth are solid, so the eddy current loss is
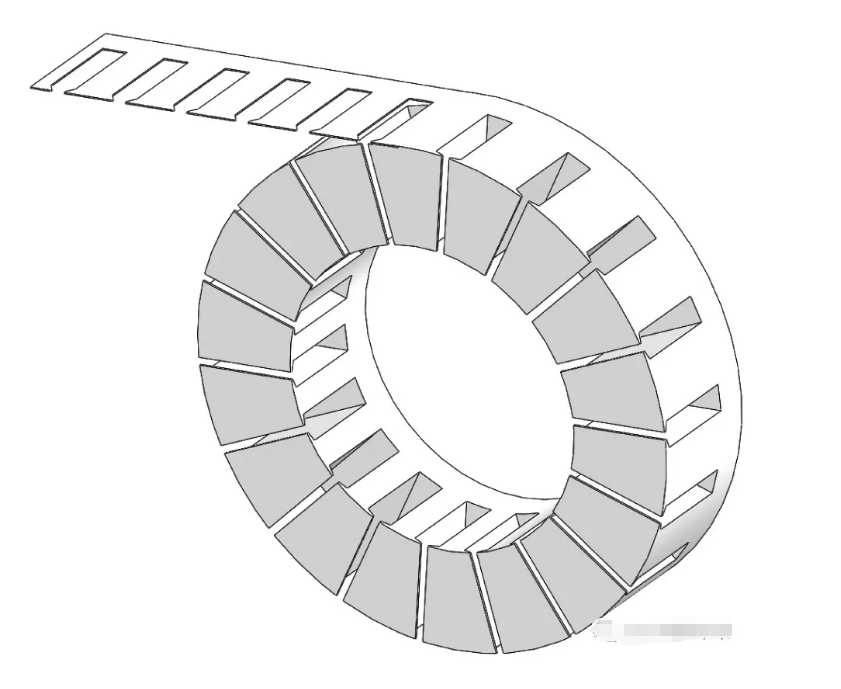
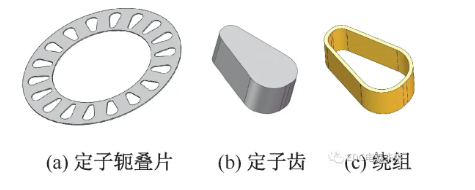
2 Motor Design
2.1 Structural characteristics
The shape of the permanent magnet inside the AFPM motor and the RFPM motor is fan-shaped structure. The inner diameter of the permanent magnet and the stator and rotor of the motor are the same as the outer diameter, and the shape of each pole flux generated by the permanent magnet is also a sector structure, and the air gap flux density of the motor changes along the radial direction. Moreover, as the radius increases, the magnetic tightness of the air gap also changes along the axial direction. Therefore, the internal magnetic field of the AFPM motor is a three-dimensional structure, and it cannot be solved simply by equating the model with a two-dimensional linear motor, but only by using the three-dimensional model to calculate its electromagnetic field. The air gap magnetism of RFPM motors only changes in the radial direction, while the air gap magnetismo remains basically unchanged in the axial direction. The waveform and size of the air gap magneticism are independent of the axis length of the motor. Therefore, the electromagnetic field solving calculation of RFPM electric motors can be used in two-dimensional models or three-dimensional models.
2.2 Research methodsThe air-gap magnetic field of AFPM motor not only changes along the radial direction, but also changes the flux density at different radius. The air-gap magnetic field is three-dimensional shape, so it is necessary to solve the three-dimensional model of AFPM motor. In addition, in order to optimize the performance of the motor, the motor structure is usually changed toTo improve the output performance of the motor, the two-dimensional model can not directly reflect the optimized new structure. The ANSYS finite element method is used to solve the transient field of AFPM motor and RFPM motor. The motor model is shown in Fig. 1.2.3 ConstraintsThis paper adopts the design index of a domestic electric vehicle range extender generator, and its design index is shown in Table 1.
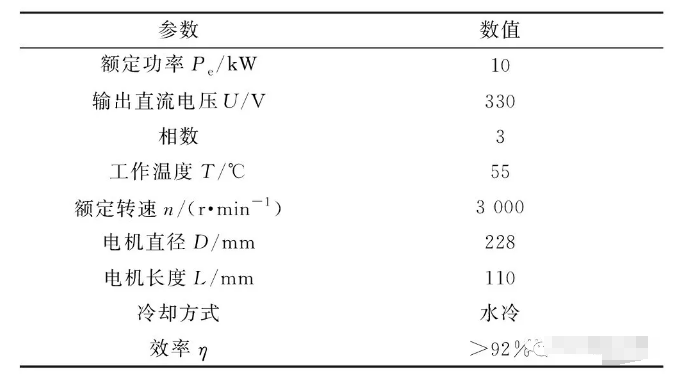
In order to make the two different topological structures of the motor comparable, but also to ensure that some technical parameters of the motor are the same, need to impose constraints on the design requirements of the motor. The constraints are as follows:
1) using the same motor material;
2) Maintain the same air gap length;
3) Keep the stator tooth magnetic density, stator yoke magnetic density, air gap magnetic density is basically the same;
4) keep the stator outer diameter basically consistent;
5) keep the heat load basically the same;6) Keep the tank full rate basically the same.
In the case of satisfying the design requirements of range extender generator and the constraints of motor comparison, the design of motor should also consider the characteristics of two different topologies. The heat load represents the internal winding heating of the motor, the internal space of AFPM motor is larger, and the heat dissipation performance is better than that of RFPM motor, but the end length of AFPM motor is longer due to the stacking of the winding ends at the inner diameter of the stator. Therefore, the stator diameter of the AFPM motor should not be too small, and the AFPM motor is usually designed as a flat structure; RFPM motors can be designed as flat or elongated structures according to dimensional formulas. Range extender generator has strict requirements on the size of the motor and should minimize the size of the motor. The output power of RFPM motor is proportional to the square of stator inner diameter. Therefore, the RFPM motor adopts flat structure to reduce the volume of motor and reduce the amount of material. The motor structure parameters are shown in Table 2.
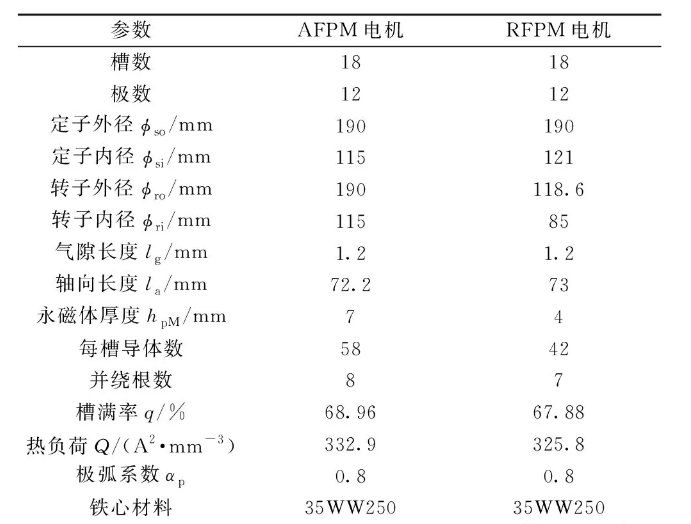
Comparison and analysis of electromagnetic properties3.1 No-load performance comparison
3.1.1 no-load counter electromotive force
The no-load counter electromotive force (BEMF) is one of the main indexes of the dynamotor. The state in service and the capacity of the dynamotor can be judged by the analysis of the waveforms and values. Fig. 6 The waveforms of no-load counter electromotive force of AFPM and RFPM are 209.34V and 208.43V respectively.
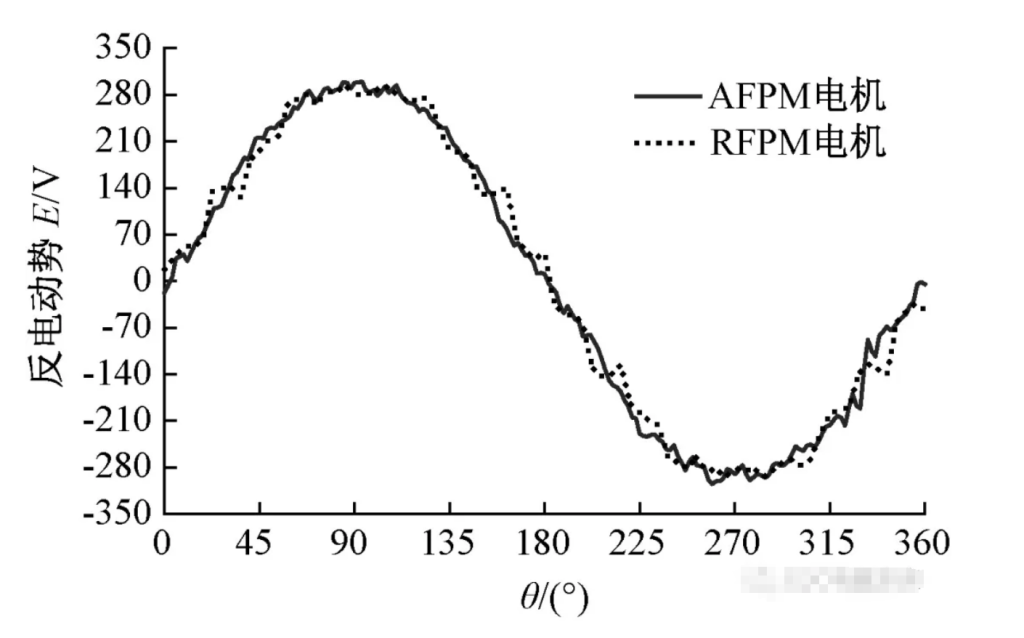
Since the air gap magnetic field of the permanent magnet synchronous motor contains high harmonics, the induced no-load counter electromotive force also contains high harmonics.

(1)In the formula: U3, U5, U7 are the valid values of the 3rd, 5th and 7th harmonic voltages; U1 is the valid value of the fundamental voltage.
Fig. 7 is the Fourier decomposition diagram of no-load counter electromotive force. As can be seen from FIG. 7, the AFPM motor has more 3rd, 5th, 9th, and 17th harmonics than the RFPM motor, while the RFPM motor has more 7th, 11th, 13th, and 19th harmonics than the AFPM motor. The total harmonic distortion rate (THD) of voltage waveform of AFPM and RFPM motors is 3.91% and 5.55%, respectively. The harmonic content of AFPM motors is less and the THD is smaller. The sinusoidal waveform of no-load counter electromotive force of AFPM motor is better than that of RFPM motor.

3.1.2 Cogging Torque
Cogging torque is the torque fluctuation caused by the change of the magnetic field energy of the permanent magnet with the change of the mechanical angle position of the rotor, which causes vibration and noise when the motor is running, thus affecting the performance of the motor. Therefore, cogging torque is one of the main indicators to measure the smooth operation of the motor. Figure 8 shows the waveform of cogging torque of AFPM and RFPM motors. The peak and peak values of the cogging torque of the two different structure motors are 14.9 N · m and 5.26 N · m, respectively, and the cogging torque of the RFPM motor is smaller.
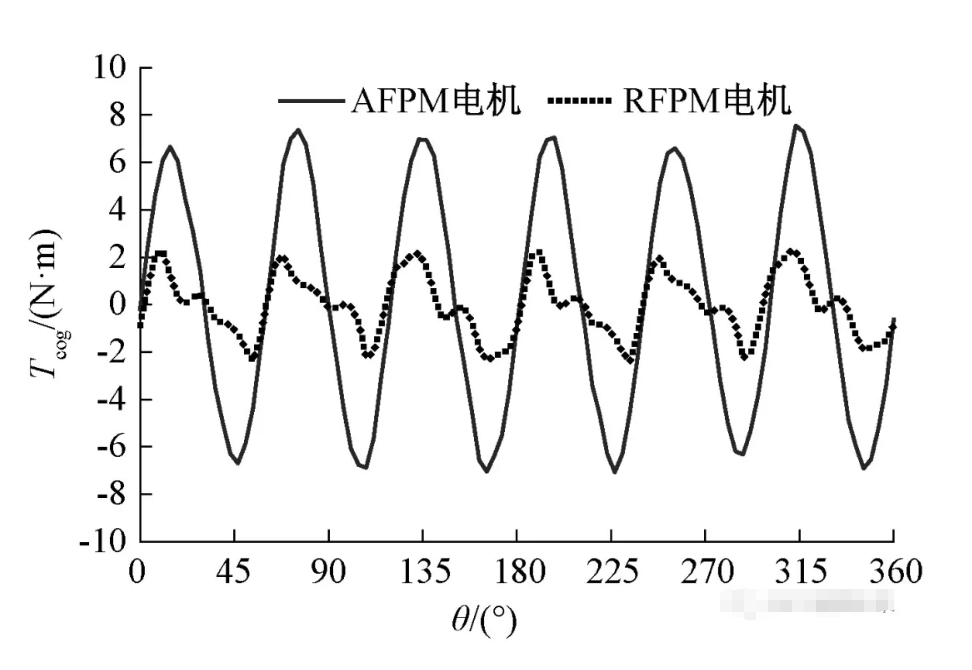
3.2 Load Performance Comparison3.2.1 Power Density
The power density S refers to the power of the unit characteristic quality of the motor, and the power density is a comprehensive parameter index to measure the design of the motor.
(2)
Where: P is the apparent power of the generator output (when the generator is connected to a pure resistance load, the power factor is approximately 1, and the apparent power of the output can be expressed by the active power of the motor output); M is the characteristic quality. Characteristic mass is the mass that can describe the electric and magnetic material quality, it is the sufficient condition to calculate the power mass density.
From equation (2), it can be seen that the calculation of the power density of the motor requires the output active power of the motor and the effective material quality of each part of the motor, and Figure 9 shows the output power waveform of the AFPM and RFPM motors when they are connected to a pure resistance load. Table 3 is the effective material quality data of each part of the motor. The average output power of AFPM and RFPM motors is 12.08 kVA and 11.21 kVA, respectively. The output power waveform of AFPM motors is larger, mainly due to the larger peak value of no-load cogging torque.
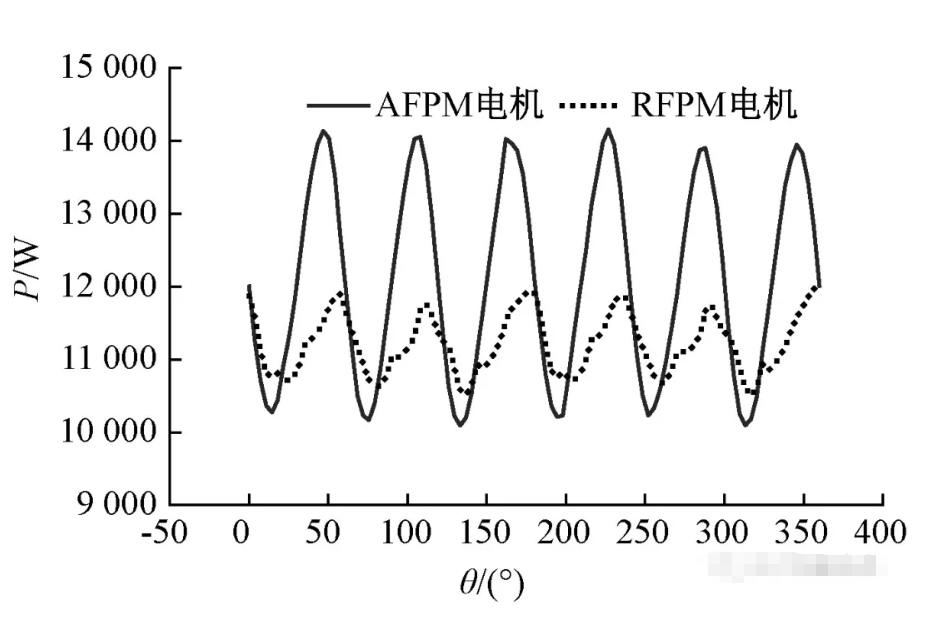
As can be seen from Table 3 and FIG. 6, the AFPM motor requires more permanent magnets than the RFPM motor to produce the same no-load counter electromotive force. In addition, the AFPM motor winding ends are longer, resulting in more winding usage. The power density of the AFPM motor and the RFPM motor is 1.175kVA / kg and 1.022kVA / kg respectively, and the power density of the AFPM motor is 14.97% higher than that of the RFPM motor. The results show that AFPM machines with single stator and single rotor structure have higher power density and higher material utilization.
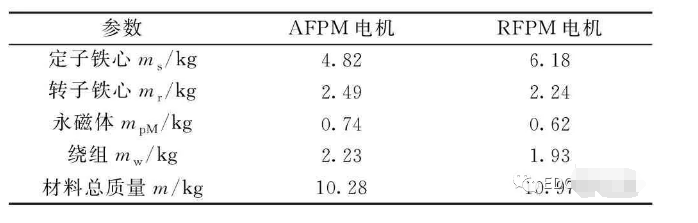
3.2.2 Efficiency Comparison at Different Speeds
Iron loss, permanent magnet eddy current loss and copper loss are the main parts of the total loss. Fig. 10 and Fig. 11 are the curves of stator and rotor core loss and permanent magnet eddy current loss at different speeds. According to FIGS. 10 and 11, the difference between the core loss and the eddy current loss of the two motors is small at low speed (< 1 000 r / min); With the increase of motor speed, the core loss of RFPM motor is much higher than that of AFPM motor, and the eddy current loss of AFPM motor is higher than that of RFPM motor. Under the condition that the magnetic densities of the tooth, yoke and air gap are almost the same, the core loss and the eddy current loss of the permanent magnet are only related to the volume of the effective material. This is the main reason why the two different topology motors have a large loss difference, from Table 3, compared to the RFPM motor, AFPM motor core material is less, the permanent magnet material is more.
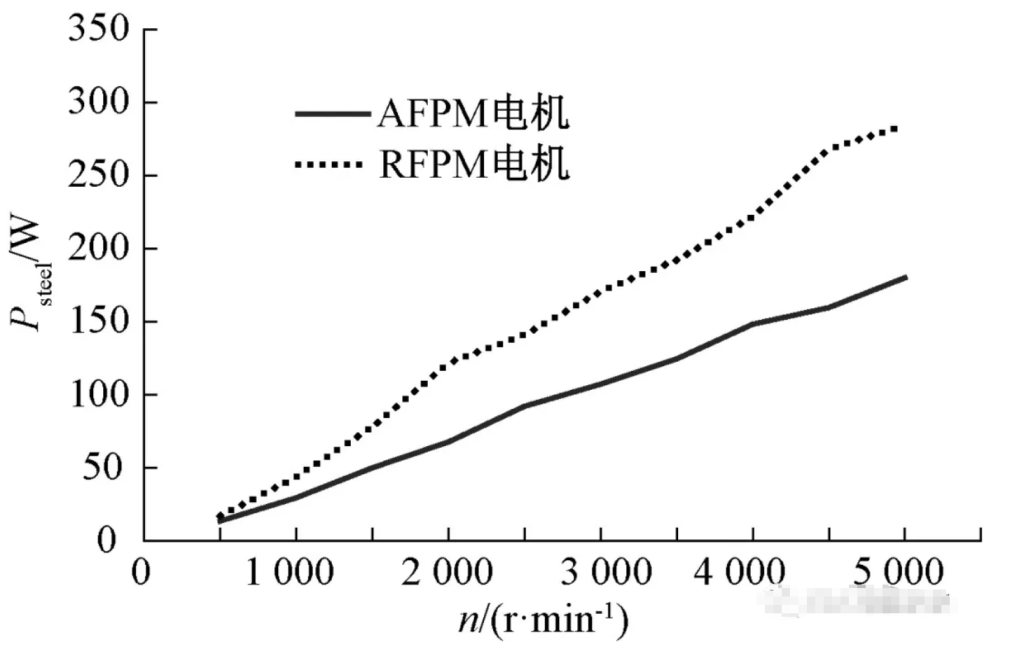
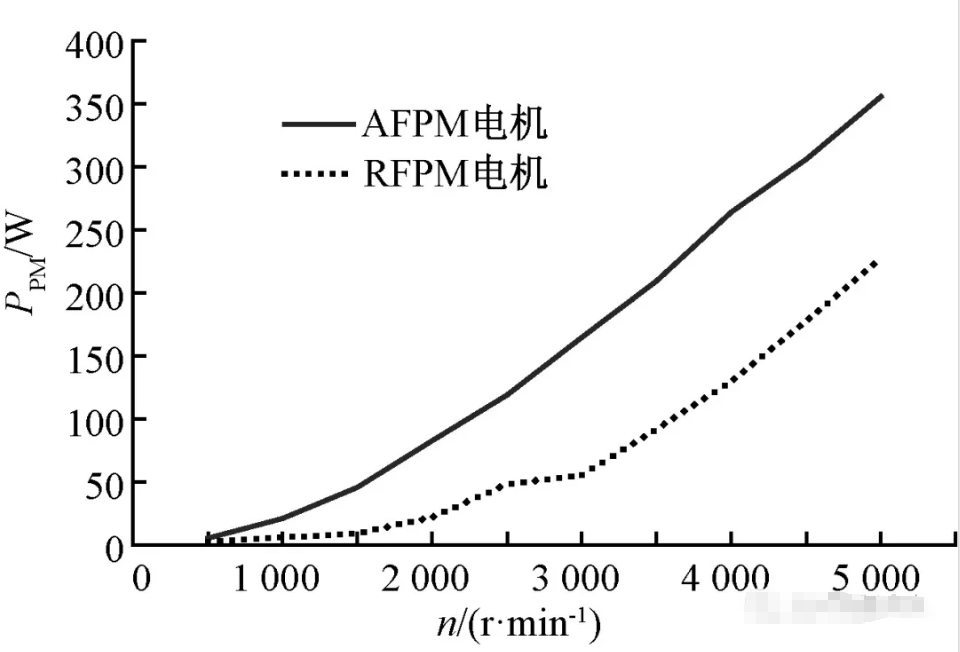
Fig. 12 shows the copper loss curve of two different topology motors at different speeds. RFPM motor uses less copper than AFPM motor, but the results show that RFPM motor winding copper consumption is slightly higher than AFPM motor. According to the formula (3), the main reason for this phenomenon is to ensure that the no-load counter electromotive force RMS, When the air-gap flux density is basically the same, the cross-sectional area of windings Ac1 is the same as the number of parallel branches a1, and the copper loss of windings is only related to the number of parallel winding Nt1. The output power of AFPM generator is slightly higher than that of RFPM generator, and the current of AFPM generator is larger than that of RFPM generator when the no-load counter electromotive force is basically the same. In addition, in order to ensure that the current density is within a certain range, the number of parallel windings of the AFPM motor is higher than that of the RFPM motor, resulting in more copper materials used in the AFPM motor, but it is smaller than the resistance of each phase of the RFPM motor, so the copper consumption of the AFPM motor winding is smaller.
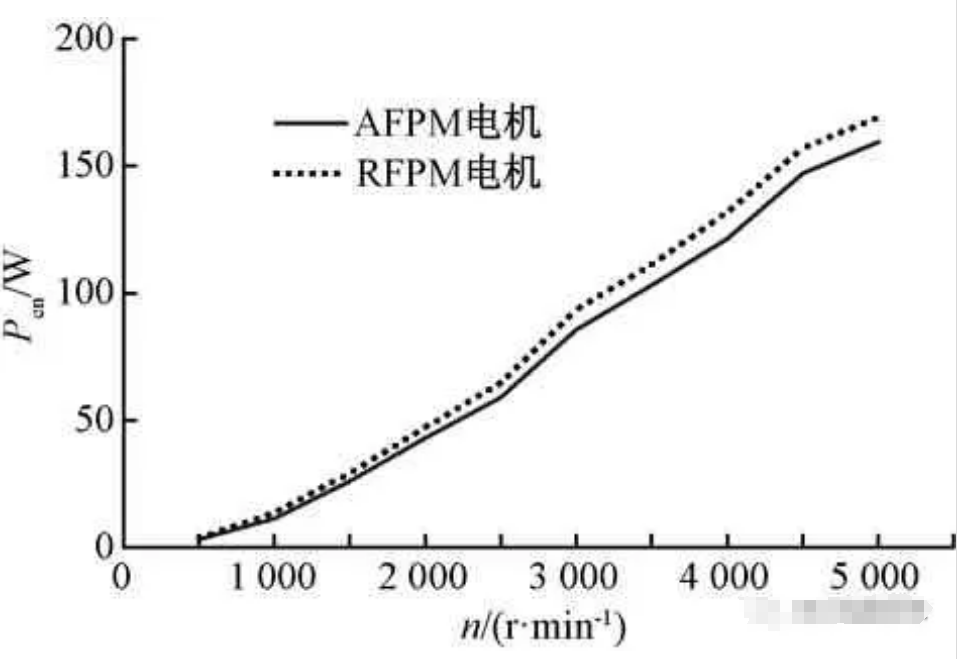
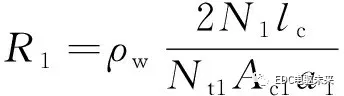
(3)
In the formula: PW is the electrical resistance of copper; N1 is the number of turns per phase in series; Average half turn length of LC winding; Nt1 is the number of coorbiting roots; Ac1 is the cross-sectional area of winding; A1 is the number of parallel branches. The motor efficiency values at different speeds are as follows:

(4)
Formula: Pout for the motor output active power; Psteel is core loss; Ppm is eddy current loss of permanent magnet; Pcoil is winding loss; PST is stray loss. Figure 13 shows the motor efficiency of two different topologies at different speeds, and Table 4 shows the motor efficiency at different speeds.
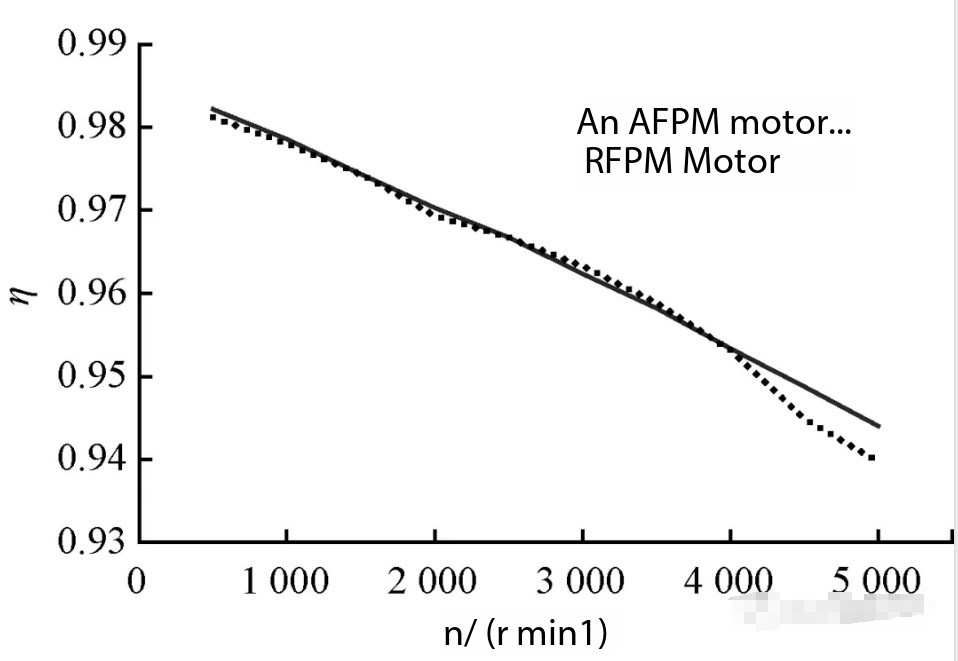
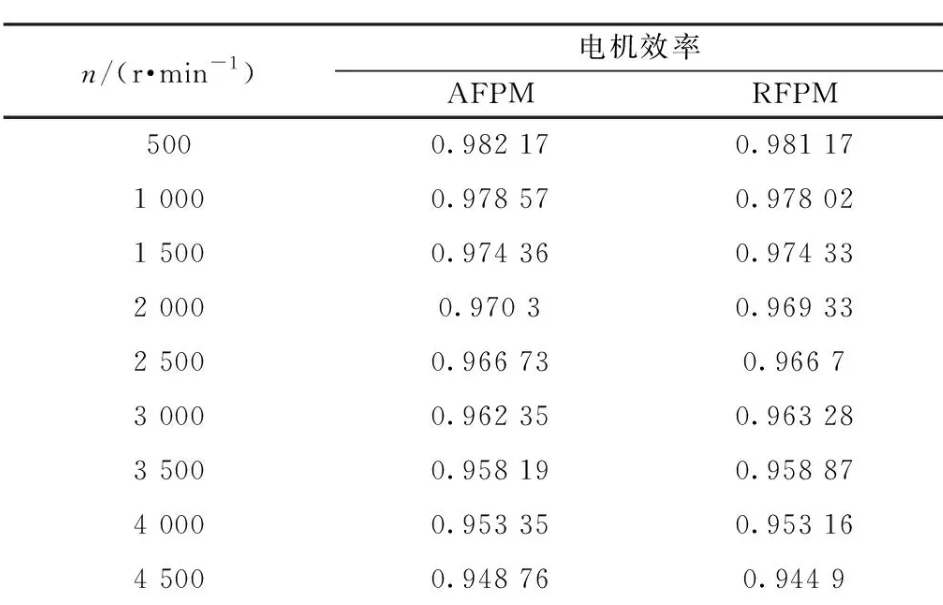
As can be seen from Figure 13, when the speed is between 500 r / min and 4 000 r / min, the efficiency of the two different topologies is basically similar. When the speed is greater than 4 000 r / min, the frequency will increase with the increase of the speed, and the stator and rotor iron core will be highly saturated. In addition, the eddy current loss of RFPM increases rapidly with the increase of the stator and rotor materials used in RFPM. AFPM motor. From Table 4, we can see that the efficiency of two different topologies is not much different at different speeds.
In summary, the power density of the AFPM motor is 14.97% higher than that of the RFPM motor, and the effective material used in the AFPM motor is less under the same power transmission. In addition, the no-load back EMF of AFPM motor has less harmonic content and better sinusoidal waveform. But AFPM motor also has the disadvantages of cogging torque and torque fluctuation, which has a great impact on the vibration and noise of the motor.
4 Performance optimization
The cogging torque peak of AFPM motor and RFPM motor are 14.9 N · m and 5.26 N · m respectively. In order to improve the stability of the output power of the motor, the cogging torque of the two motors with different topologies is optimized by means of stator opening auxiliary grooves. The optimized motor stator model is shown in Figure 14.
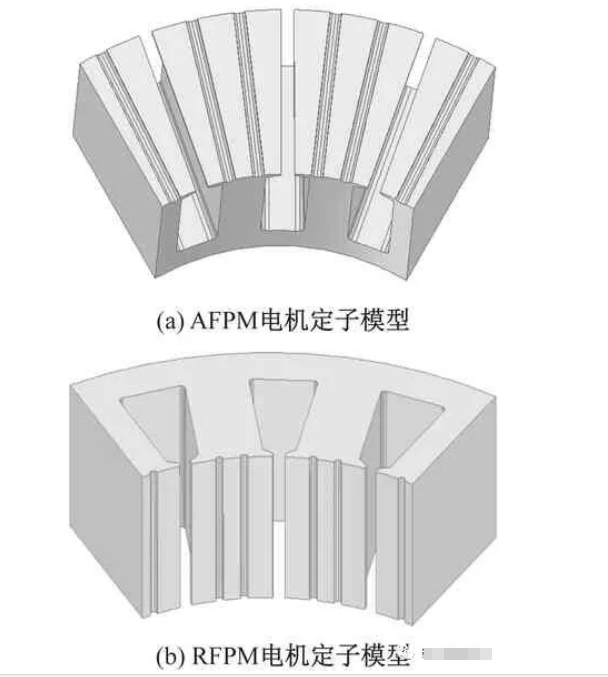
FIG. 15 is a waveform diagram of the optimized rear cogging torque. The peak and peak value of the cogging torque of the AFPM motor and the RFPM motor after optimization are 2.66 N · m and 1.65 N · m, as can be seen from Figure 15. The motor’s rod torque was effectively reduced by fixed teeth opening auxiliary grooves, where the AFPM motor’s torque peak was reduced from 14.9 N · m before optimization to 2.66 N · m after optimization, and the optimization effect was relatively obvious, while the RFPM motor’s port torque peaks were small.
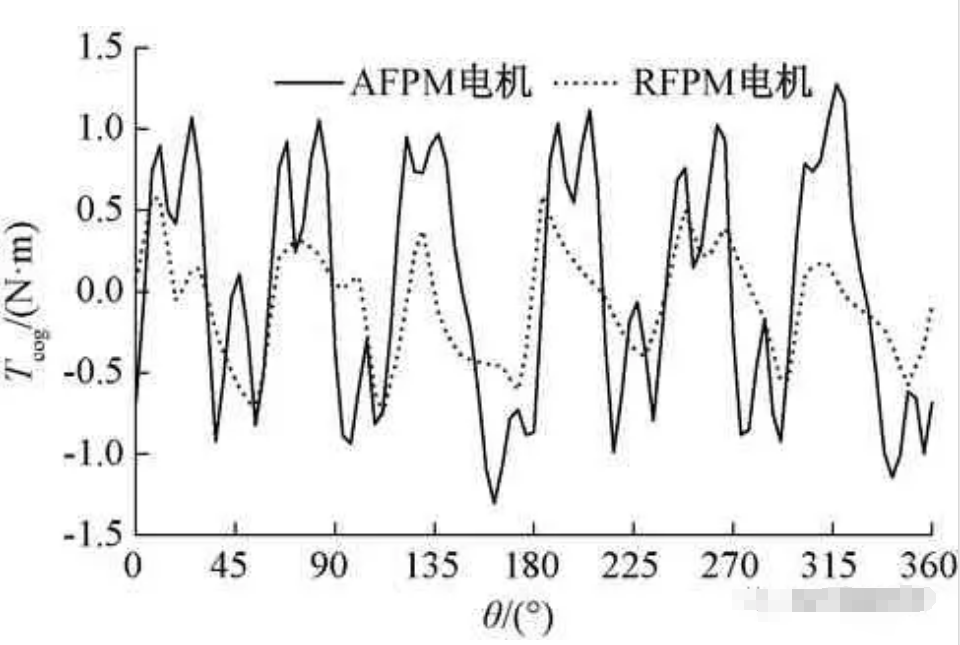
The electromagnetic performance of two different topologies after optimization is shown in Table 5. From Table 5, it can be concluded that: (1) The auxiliary grooves in the stator teeth can improve the air-gap magnetic field waveform and reduce the harmonic content in no-load counter electromotive force. The harmonic distortion ratio of no-load counter electromotive force of AFPM and RFPM is decreased, and the sinusoidal waveform of AFPM is better; (2) The output power of AFPM motor and RFPM motor are reduced, but the power density of AFPM motor is 13.19% higher than that of RFPM motor; (3) The efficiency of the two different topologies of the motor is basically the same.
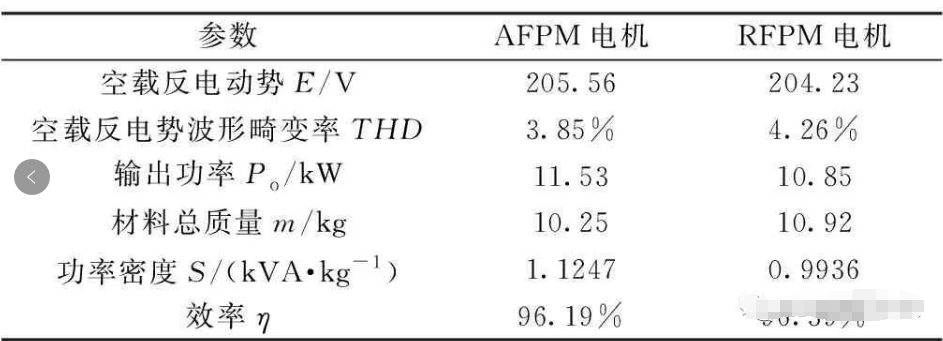
5 Conclusion
In this paper, the electromagnetic performance of AFPM motor and RFPM motor under no-load and load conditions is compared and analyzed. The results show that the cogging torque and torque ripple of AFPM motor are larger than those of RFPM motor, but the waveform of no-load counter electromotive force is sinusoidal and the power density is higher. In addition, the AFPM motor rotor disc can replace the range extender flywheel part, greatly saving manufacturing costs, AFPM motor can become one of the strong competitors of the range extender motor.