How can motor iron consumption be reduced?
Factors affecting basic iron consumption
Analyze the problem we first know some basic theory, which helps us understand. First of all, we need to know two concepts, one is the alternating magnetization to give a simple statement is the motor stator or rotor teeth occurring; one is the nature of the rotating magnetization, is the motor stator or rotor yoke produced. There are many articles from two points in accordance with the above solution to calculate the iron consumption of the motor based on different characteristics. Tests have shown that the following phenomena exist for silicon steel sheets under magnetization of both natures:
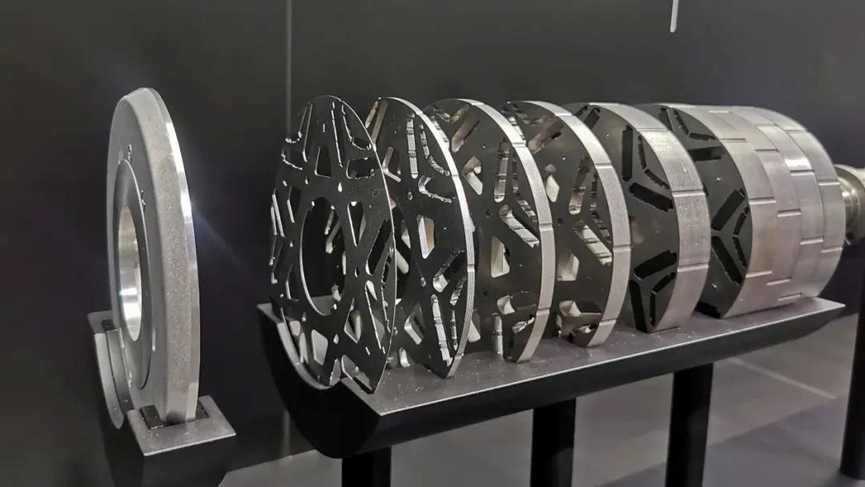
When the magnetic flux density is below 1.7 Tesla, the hysteresis loss caused by rotational magnetization is larger than that caused by alternating magnetization; when it is higher than 1.7 Tesla, it is the opposite. Motor yoke flux density is generally in 1.0 ~ 1.5 Tesla, the corresponding rotational magnetization hysteresis loss than the alternating magnetization hysteresis loss of about 45 ~ 65%.
Of course, the above conclusions are also brought to the individual did not actually go through the verification. In addition, the magnetic field in the core changes, in which the current will be generated, known as eddy current, which causes the loss is called eddy current loss. In order to reduce the eddy current loss, the motor core usually can not be made into a whole piece, but by each other insulated sheet of steel along the axial stacked up, in order to impede the flow of eddy current. Specific iron consumption formula here will not be burdensome, we Baidu iron consumption calculation of the basic formula as well as the meaning will be very clear. The following analysis of several major impact on our iron consumption of the key points, so that we can also be applied in the actual project when the problem of forward or reverse thrust.
After talking about the above again why does the manufacture of punched sheets why does it have an impact on iron consumption? Punching process characteristics are mainly based on different shapes of punches, according to different types of holes and slots demand, to
determine the corresponding shear mode as well as the stress level, and then to ensure that the stacked sheet periphery of the shallow stress region of the conditions. Because of the depth and shape, it is often affected by sharp angles such that high stress levels can cause great iron damage conditions in the shallow stress areas, especially in that part of the stack where the shear edge is relatively long in the range. Specifically, this occurs mainly in the notch region, and therefore tends to be a point of interest in the actual research process. Low-loss silicon steel sheet is often determined by the larger size of the grain, the impact will be in the bottom edge of the punch sheet with synthetic burr and tearing shear, and the angle of impact will affect the size of the burr, the deformation area caused by the obvious impact.
If a high stress area, along the edge of the deformation area has been extended to the interior of the material, then these areas of the grain structure is bound to change accordingly, will be twisted or fracture, and along the direction of the tear to produce extreme elongation of the boundary, then the shear direction of the stress area grain density is bound to increase, which leads to a corresponding increase in the region of the internal iron loss.
Therefore, at this time, the material in the stress region can be treated as a high loss material along the edge of the impact on the ordinary laminated above, in this way, the actual constants can be determined down to the edge of the material, the use of the iron loss model on the edge of the impact of the actual loss to carry out further determination.
1 annealing process on the impact of iron loss
Iron loss conditions mainly exist in the silicon steel sheet, and mechanical and thermal stress will change with its own actual characteristics and affect the silicon steel sheet, additional mechanical stress will lead to iron loss changes in the situation. At the same time, the continuous increase of the internal temperature of the motor will also contribute to the emergence of the iron loss problem. Take effective annealing measures to remove the additional mechanical stress, will have a favorable impact on the reduction of iron loss in the motor.
2 manufacturing process causes high loss reasons
Silicon steel sheet as the motor’s main magnetic materials, its performance in line with the performance of the motor has a great impact, mainly to ensure that the grade of silicon steel sheet in line with the design requirements, in addition to the same grade of silicon steel sheet of different manufacturers of material performance has a certain degree of variability in the selection of materials should try to select a good silicon steel manufacturer’s materials. Here are some key factors that affect the iron consumption before the actual encounter.
(1) Silicon steel sheet is not insulated or not well treated. This type of problem can be found in the silicon steel sheet testing process, but not all motor manufacturers have the testing program, the problem is often not well recognized in the motor manufacturers.
(2) Damaged insulation between sheets or short circuit between sheets. This type of problem occurs in the manufacturing process of the iron core. If the core stacking pressure is too large, so that the insulation between the pieces is damaged; or punching piece punching burrs are too large, remove burrs by grinding, resulting in serious damage to the surface insulation of the punched piece; and core stacking is completed after the slot is not light, the use of repair filing; or due to the stator bore is not light, the stator bore and the seat stop is not concentric, and other factors such as the use of turning to correct the way. These motor production and processing process of the usual use of the motor performance, especially iron loss has a great impact.
(3) with fire or electric heating and other methods to remove the winding, resulting in overheating of the iron core, so that the permeability of the magnetic properties of the decline and damage to the insulation between the pieces. The problem mainly occurs in the production process of winding repair and motor repair process.
(4) Stacked welding and other processes will also cause damage to the insulation between the stacked pieces, increasing eddy current losses.
5) Insufficient iron weight is not compacted between the pieces. The end result is that the weight of the iron core is insufficient, the most direct will lead to the current is too poor, at the same time there will be the fact that iron loss exceeds the standard.
(6) silicon steel sheet paint is too thick to cause the magnetic circuit is too saturated, the relationship between no-load current and voltage curve is bent more seriously. This is also a key element of the silicon steel sheet production process.
(7) core production and processing process will cause silicon steel sheet punching and shearing surface attachment grain orientation damage, resulting in the same magnetic susceptibility under the increase in iron loss; for frequency conversion motor and consider the additional iron loss brought about by harmonics; this is the design of the link should be a comprehensive consideration of the factors.
In addition to the above factors, the design value of the motor iron loss should be synthesized core production and processing of the actual, try to achieve the theoretical value and the actual value of the fit. General material suppliers to provide the characteristic curve in accordance with the Epstein square circle method measured, and different parts of the motor in the direction of magnetization is not the same, this special rotating iron loss currently can not be taken into account. This, to varying degrees, leads to inconsistencies between calculated and measured values.
Engineering ways to reduce iron loss
There are many ways to reduce iron loss on engineering, and the most important thing is to get it right. Of course not only the problem of iron loss, other losses are like this. The most fundamental way is to know the cause of iron loss, is the high magnetic density or frequency or local saturation is too serious and so on. Of course, in accordance with the normal way is on the one hand from the simulation side as close as possible to the real, on the other hand, the process with technology to reduce the additional iron consumption. According to the most common way is to increase the replacement of good silicon steel sheet, regardless of cost, you can choose to import the super silicon steel. Of course, with the development of domestic new energy drive technology has also led to better development of upstream and downstream. Domestic steel mills are also launching specialized silicon steel products. Spectrum for different application scenarios have a better classification of products. Here are a few examples of encountered more direct method:
1. Optimize the magnetic circuit
Optimize the magnetic circuit, to be precise, is to optimize the sinusoidal nature of the magnetic field. This is very critical, not only the fixed frequency induction motor to do. Inverter induction motors synchronous motors are critical. I have been in the textile machinery industry in order to reduce the cost of two different performance of the motor, of course, the main thing is the presence or absence of oblique pole, resulting in the air gap magnetic field sinusoidal inconsistency. Because the work in high-speed conditions, iron consumption accounted for a relatively large, so that the loss of the two motors is a big difference, and finally after a number of columns of backward calculation due to the control algorithm under the motor’s iron consumption difference of more than 2 times. Here also reminds us to do frequency control motor must be coupled to do the control algorithm.
2. Decrease magnetic density
Increase the length of the iron core or increase the magnetic area of the magnetic circuit to reduce the magnetic flux density, but the amount of iron used in the motor increases.
3. Reduce the thickness of the iron chip to reduce the loss of induced current.
Such as cold rolled silicon steel instead of hot rolled silicon steel can reduce the thickness of silicon steel, but the thin iron chip will increase the number of iron chips and motor manufacturing costs.
4. The use of cold rolled silicon steel sheet with good magnetic conductivity to reduce hysteresis loss.
5. Adopting high-performance iron chip insulation coating.
6. Heat treatment and manufacturing technology.
The residual stress after iron chip processing will seriously affect the loss of the motor, silicon steel sheet processing, cutting direction, punching and shearing stress on the core loss of the greater impact. Cutting in the direction of the milling of silicon steel sheet, and heat treatment of silicon steel punching can reduce the loss of 10% to 20% and other methods to achieve.