Classification and requirements of industrial robots motor drive systems
Robot electric servo drive systems are actuators that utilize torque and force generated by various electric motors to directly or indirectly drive the robot body to obtain various motions of the robot.
The electric motor for industrial robot joint drive requires maximum power-to-mass ratio and torque-to-inertia ratio, high starting torque, low inertia, and wider and smoother speed regulation range. Especially like the robot end-effector (hand claw) should be used as small as possible volume, mass of the motor, especially when the requirements of rapid response, servo motors must have high reliability and stability, and has a large short-term overload capacity. This is a prerequisite for the application of servo motors in industrial robots.
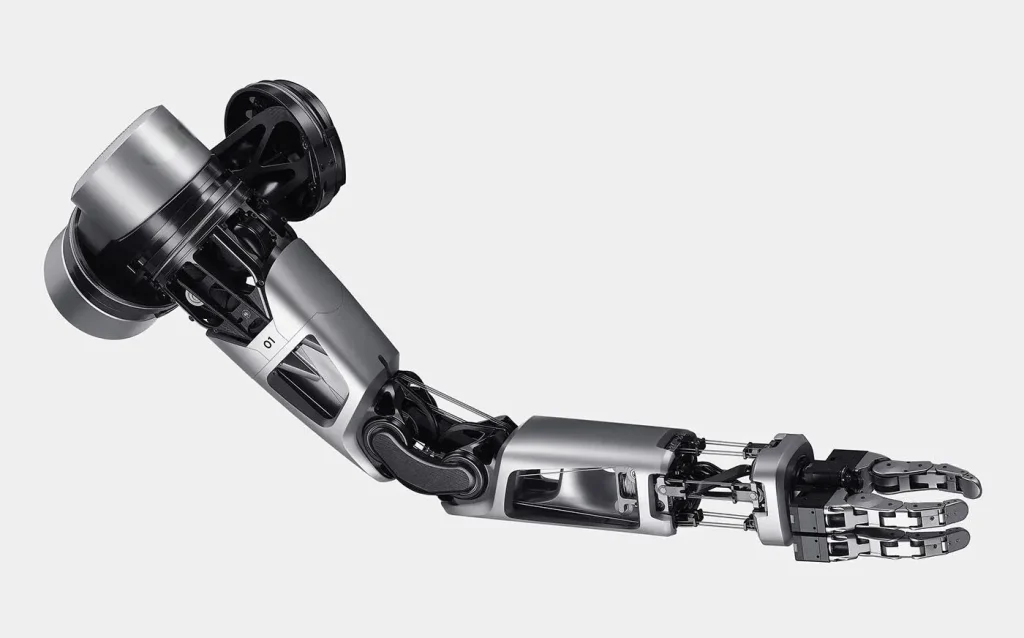
1. The main requirements of the robot on the joint drive motor
1) Rapidity
Motor from the command signal to complete the instruction required by the working state of the time should be short. Response to the command signal the shorter the time, the higher the sensitivity of the electric servo system, the better the fast response performance, generally to the size of the servo motor electromechanical time constant to illustrate the servo motor fast response performance.
2) Starting torque inertia ratio is large
In the case of driving loads, the starting torque of the servo motor of the robot is required to be large, and the moment of inertia is small.
3) Continuity and linearity of control characteristics
With the change of the control signal, the motor speed can be continuously changed, and sometimes the speed is also required to be proportional or approximately proportional to the control signal.
4) Wide speed control range, it can be used in the speed range of 1:1000~10000.
5) Small size, small mass, short axial size.
6) The motors can withstand harsh operating conditions and carry out very frequent forward and reverse and acceleration and deceleration operation, and can withstand overload in a short period of time.
At present, since AC and DC servo motors with high starting torque, large torque and low inertia are widely used in industrial robots, most of the industrial robots with a general load of 1000N (equivalent to 100kgf) or less are driven by electric servo drive systems. The joint drive motors used are mainly AC servo motors, stepper motors and DC servo motors. Among them, AC servo motors, DC servo motors, and direct drive motors (DD) all utilize closed-loop position control and are generally used in high-precision, high-speed robot drive systems. Stepping motor drive system is mostly used in the open-loop system of small and simple robots that do not require high precision and speed. AC servo motors are widely used in flammable and explosive environments due to electronic commutation without commutation sparks. The power range of robot joint drive motors is generally 0.1 to 10kW.
2. The motor used in the robot drive system
The motors used in the industrial robot drive system can be roughly subdivided into the following categories:
1) AC servo motor, including synchronous AC servo motors and reactive stepping motors.
2) DC servo motor, including small inertia permanent magnet DC servo motor, printed winding DC servo motor, large inertia permanent magnet DC servo motor, hollow cup armature DC servo motor.
3) Step motor, including permanent magnetic induction stepping motor.
Speed sensors are mostly used in speed generators and resolvers, position sensors are mostly used in photoelectric code disks and resolvers. In recent years, foreign robot manufacturers have been using a set of photoelectric code disk and resolver function as one of the hybrid photoelectric position sensor, servo motor can be with the position and speed detector, brake, deceleration mechanism composed of servo motor drive unit. The robot drive system requires a drive system with low clearance, high stiffness, high output torque, and a large reduction ratio.
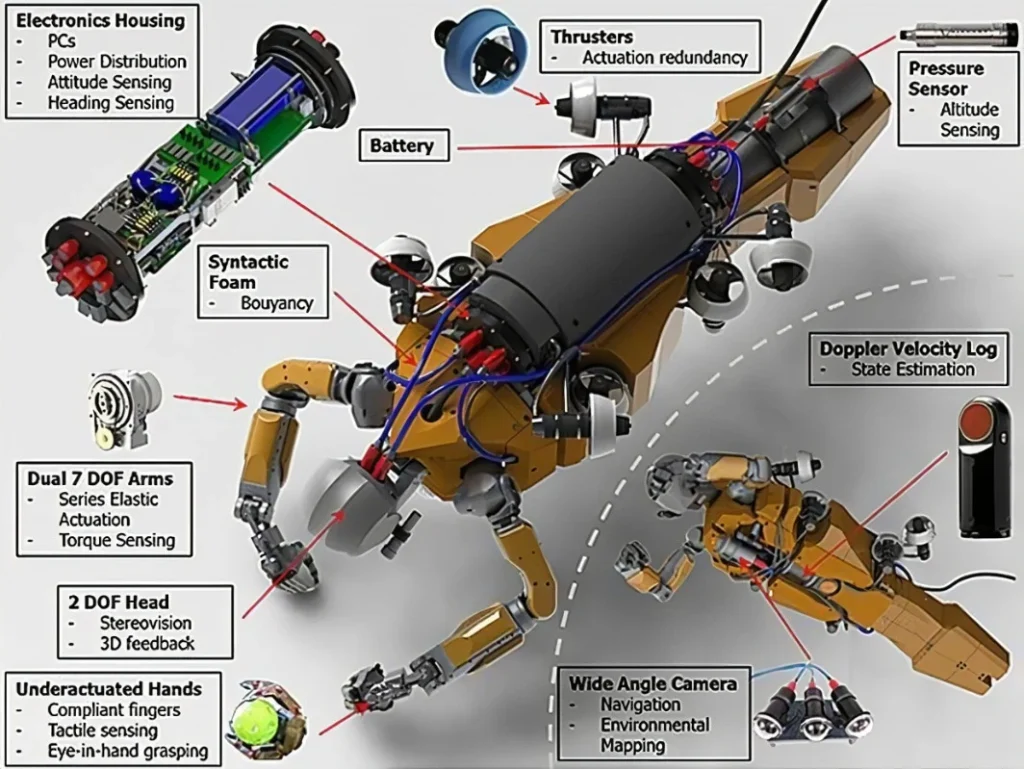
3. The commonly used reduction mechanism
RV reduction mechanism, Harmonic reduction mechanism, Cycloid reduction mechanism, Planetary gear reduction mechanism, Side-backlash-free reduction mechanism, Worm gear reduction mechanism, Ball screw mechanism, Metal belt/tooth reduction mechanism, Ball reduction mechanism.
The general structure of the electric servo system for industrial robots is three closed-loop control, i.e., current loop, speed loop and position loop.
At present, many motor manufacturers have developed and AC servo motor compatible drive products, users focus on different functions according to their own needs and choose a different servo control mode, in general, AC servo drive, can be manually set through its internal function parameters to achieve the following functions:
Position control mode, Speed control mode, Torque control mode, Position, speed mixed mode, Position, torque mixed mode, Speed, torque mixed mode, Torque limitation, Position deviation excessive alarm, Speed PID parameter setting, Speed and acceleration feed forward parameter setting, Zero drift compensation parameter setting, Acceleration and deceleration time setting, etc.
4. Driver type
1) DC servo motor drive
DC servo motor drive mostly used pulse width modulation (PWM) servo drive, by changing the pulse width to change the average voltage added to both ends of the motor armature, thereby changing the speed of the motor.
PWM servo drive has a wide speed range, good low-speed characteristics, fast response, high efficiency, overload capacity, etc., often used as a DC servo motor drive in industrial robots.
2) synchronized AC servo motor drive
Compared with DC servo motor drive system, synchronous AC servo motor drive has the advantages of high ratio of rotating moment of inertia, no brush and commutation sparks, etc., which is widely used in industrial robots.
Synchronous AC servo motor drive usually adopts current-type pulse width modulation (PWM) phase inverter and multi-closed-loop control system with current loop as the inner loop and speed loop as the outer loop to realize the current control of three-phase permanent magnet synchronous servo motor. According to its working principle, drive current waveform and control mode, it can be divided into two kinds of servo systems:
(1) Rectangular wave current driven permanent magnet AC servo system.
(2) Sinusoidal current-driven permanent magnet AC servo system.
The permanent magnet AC servo motor driven by rectangular wave current is called brushless DC servo motor, and the permanent magnet AC servo motor driven by sinusoidal wave current is called brushless AC servo motor.
3) Step motor driver
Stepping motor is a component that transforms electric pulse signals into corresponding angular or linear displacements, and its angular and linear displacements are proportional to the number of pulses. The rotational speed or linear speed is proportional to the pulse frequency. Within the range of load capacity, these relationships do not change due to fluctuations in supply voltage, load size, environmental conditions, and the error does not accumulate over time, the stepper motor drive system can be used to regulate the speed by changing the pulse frequency over a wide range, realizing fast starting, forward and reverse braking. As an open-loop digital control system, it is more widely used in small robots. However, due to its poor overload capacity, relatively small speed range, pulsation, unbalance and other shortcomings of low-speed movement, generally only used in small or simple robots.
4) Direct drive
The so-called direct drive (DD) system is the motor and its driven load directly coupled together, there is no deceleration mechanism.
Compared with the traditional motor servo drive, DD drive reduces the reduction mechanism, thus reducing the gap and looseness generated by the reduction mechanism during the system transmission, greatly improving the accuracy of the robot, and also reducing the friction of the reduction mechanism and the reduction of robot control accuracy caused by the transmission torque pulsation. The DD drive, because of the above advantages, has good mechanical rigidity, can be high-speed and high-precision action, and has fewer parts, simple structure, easy maintenance, high reliability and so on, and is attracting more and more attention in the application of high-precision, high-speed industrial robots.
As the key link of DD drive technology is DD motor and its driver. It should have the following characteristics:
(1) Large output torque: 50 to 100 times of the output torque of servo motor in traditional drive mode.
(2) Small torque pulsation: the torque pulsation of DD motor can be suppressed within 5% to 10% of the output torque.
(3) Efficiency: Compared with motors using reasonable impedance matching (under conventional drive), DD motors are operated under usage conditions where power conversion is poor. Therefore, the larger the load, the greater the tendency to choose a larger motor.
At present, DD motors are mainly categorized into variable reluctance type and variable reluctance hybrid type with the following two structural types:
(1) Variable reluctance type DD motor with double stator structure;
(2) Variable reluctance hybrid DD motor with central stator type structure.