Analysis of Axial Flux Permanent Magnet Motors application
The technological innovation and mass production application of axial flux motors may effectively solve some of the outstanding problems currently faced by the electric vehicle field, such as lightweight, torque density and people’s most concerned about the range. In the Vision One Eleven concept car just released by Mercedes-Benz, as well as the Ferrari SF90 Stradale, 296GTB and McLaren Artura and other high-performance models that have come out before, the entire drive system is equipped with axial flux motors, which are also regarded by major ultra-luxury automobile brands as “the best solution for the electrification of high-performance cars”.
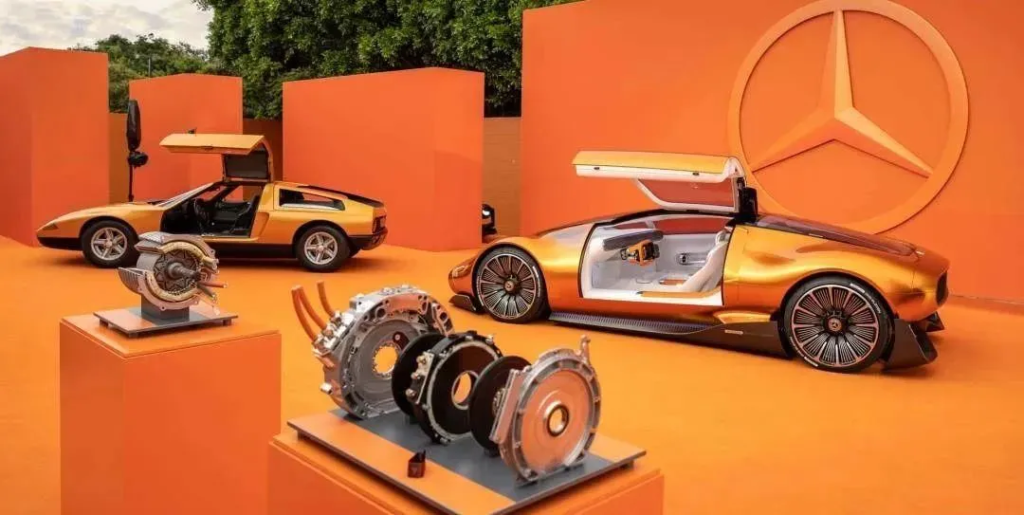
While radial flux motors have brought the entire automotive industry into the age of electrification, axial flux motors are better in every way: not only are they lighter and smaller, but they also deliver more torque and more power, a breakthrough motor that creates more punch in a smaller, lighter body, opening up a whole new world of possibilities for automotive designers.
The torque of a radial flux motor is proportional to the square of the rotor radius, whereas the torque of an axial motor is proportional to the cube of the rotor radius, so it can produce higher torque figures; at the same output power, an axial flux motor is 50% smaller and 50% lighter than a radial flux motor, such as the axial flux motor in the Mercedes-Benz Vision One-Eleven pure-electric concept car. For example, the weight of the axial flux motor equipped in the Mercedes-Benz Vision One-Eleven pure electric concept car is only 1/3 of the weight of an ordinary motor with the same output power.
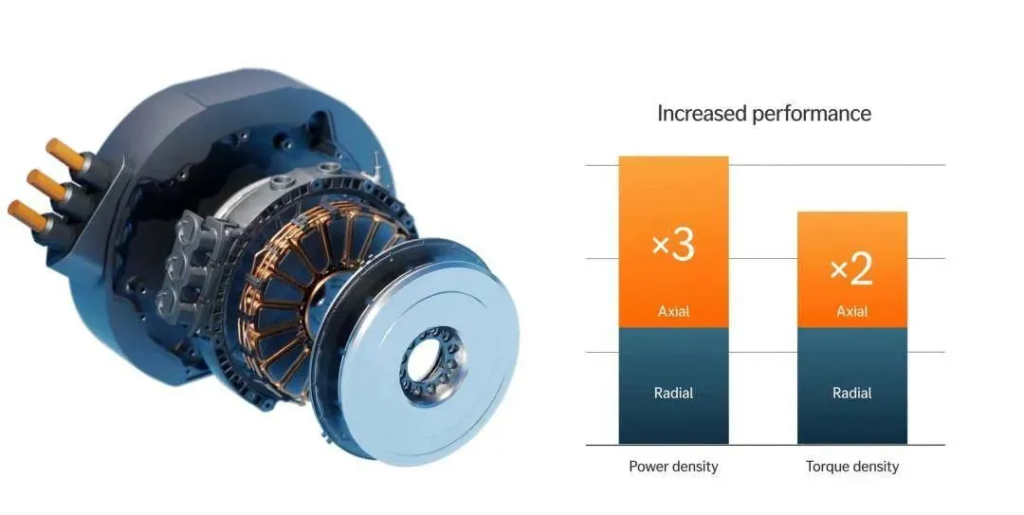
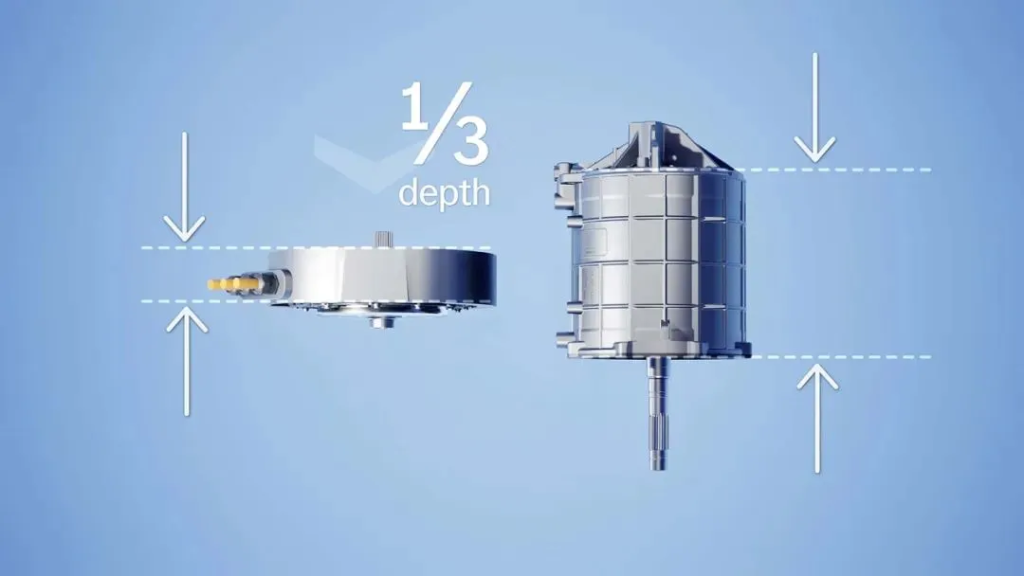
The advantage in size and weight not only greatly reduces the use of materials such as copper, iron and permanent magnets required for the production of motors, but it also allows the axial flux motor to be arranged in more confined places, such as the notch in the wheel hub of an automobile, which reduces the involvement of components such as gearboxes and driveshafts, and reduces the loss of kinetic energy, and so the drive efficiency is higher and the torque compensation effect is more direct.
Also, because the axial flux motor is so compact and lightweight, less structure is needed to mount it, which saves even more weight, and it doesn’t reach as high a speed as a conventional radial flux motor, so there can be no reduction gears, which further reduces the total system weight, and other subsystems can benefit from the weight reduction, such as the brakes and cooling system. Overall, a 5-10% improvement in efficiency and range can be realized.
Mercedes-Benz Axial Flux Drive Motor Technology Revealed
Mercedes-Benz has just unveiled its new concept sports car, the Vision One Eleven, which, in addition to its unique styling and design, is equipped with four drive motors, each of which produces 480 hp, giving the car a maximum output of 1,920 hp. Equipped with YASA’s next-generation axial-flow motors, which were acquired by Mercedes-Benz in October 2021 and will be produced at Mercedes-Benz’s Berlin-Marienfeld plant, they will be the centerpiece of the next powertrain in the performance segment.

Currently 99% of electric vehicles are equipped with radial flux motors, but YASA’s axial flux motors are 1/3 the depth of radial flux motors, and 1/3 the weight due to fewer components.What’s more, the compact motors produce 480 hp each, which is 145 hp more than comparable motors developed by Koenigsegg.
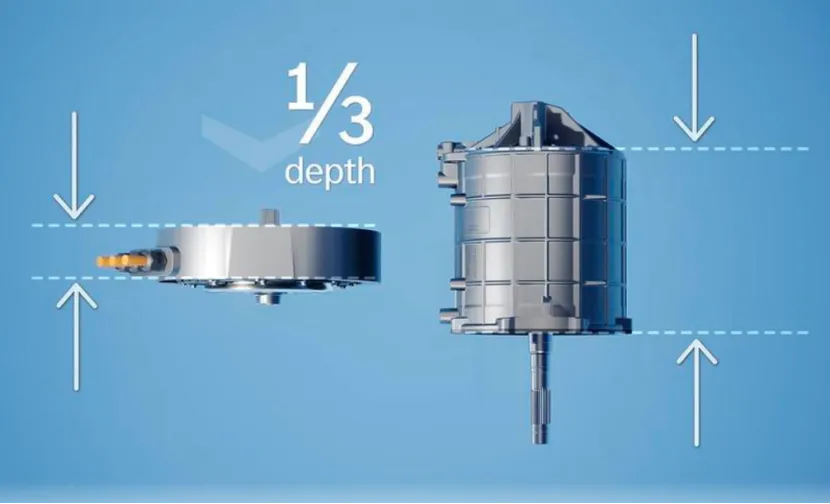
Tim Woolmer, Founder and CTO of YASA, said, “In a traditional radial flux motor, the current is perpendicular to the axis of rotation, whereas in an axial flux motor, the electromagnetic current is highly efficient because it flows and rotates parallel to the motor’s axis, and it is more powerful, more durable, and capable of a whole new level of performance when compared to a radial flux motor. “
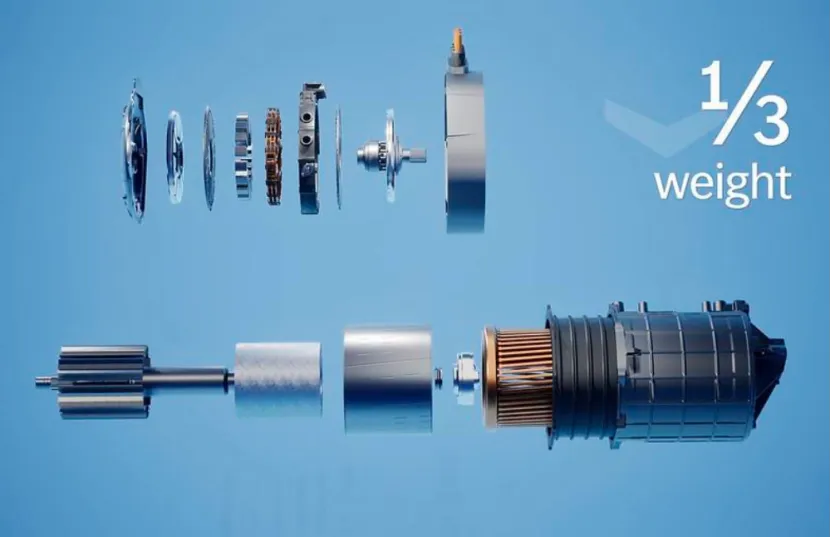
The benefits of this axial flux motor are not just “weight and size” but also increased freedom of installation. The motor, which previously had to be mounted in the front and rear center of the vehicle, can now be mounted inside the wheels and can be used as a brake to store power efficiently and as a caliper as well. As there is no need to mount the motor on the body side, there is more space in the cabin and luggage compartment, and the design freedom of the body itself will be increased. The benefits of this axial flux motor are not just “weight and size”, but also “high mounting freedom”.
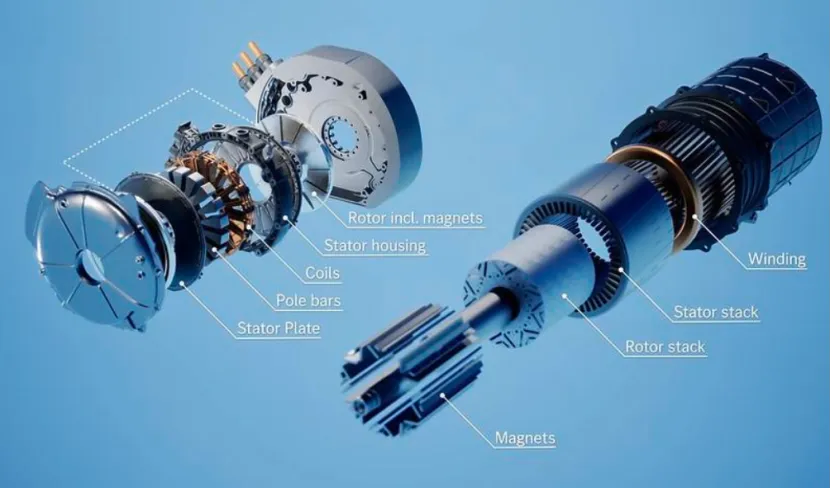
If the idea is even more daring, it is possible to remove the engine, transmission, exhaust system, etc. from a gasoline car, mount this axial flux motor on each wheel, and install batteries and inverters in the empty space somewhere to quickly create an electric car, or use a gasoline car platform to create a cheap electric car.
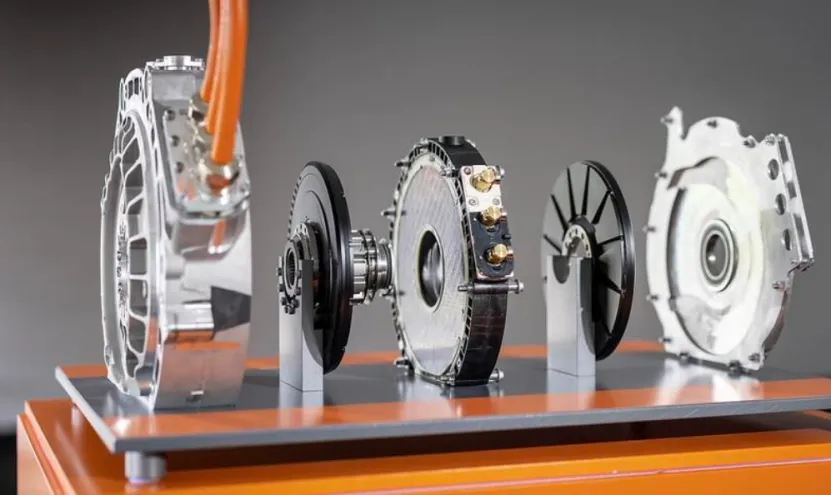
Of course, torque vectoring of the wheels can also be done with more efficient and simpler systems. Because there is no need to install differentials and driveshafts, the front and rear wheels can move much more, and it will be possible to realize unprecedented automotive motion. Torque vectoring has always been a passive control that “brakes the inner ring and increases the torque of the outer ring relative to the outer ring,” but with this axial flux motor, it will be possible to control the front and rear drive more freely, and it will be possible to realize a completely different dimension of performance. In other words, this axial flux motor has unlimited potential to do things that gasoline-engine vehicles are unable to do, and to realize layouts that are not possible with conventional radial flux motors. Not only will there be maneuverability, but interior space and carrying capacity will be greatly increased.
Electric vehicle startup Infinitum
Launches Aircore Mobility motor3
Electric vehicle startup Infinitum has launched the Aircore Mobility motor3, an axial flux propulsion and traction motor designed to provide more sustainable power for passenger and commercial electric vehicles, as well as other emerging electric platforms such as aviation, marine and construction equipment. According to Infinitum, the Aircore Mobility motor is 10 percent more efficient, 50 percent smaller and lighter than radial flux motors with equivalent torque ratings. The axial flux motor design achieves this through the use of patented PCB stator technology, which requires 66% less copper without the need for a heavier core.
Increased efficiency and reduced weight means longer range ranges, smaller and cheaper battery packs and faster charging times for electric vehicles and other electric platforms.
Axial Flux Motor Technology
Most electric motors are some variation of radial flux motors, which use an iron-core stator and windings to create a rotating magnetic field that moves the rotor within the stator. Iron helps to concentrate and increase the strength of the magnetic field, but it is heavy and adds a lot of weight to the motor. In an axial flux motor, the rotor disk is located next to the stator and the axial magnetic force (a force parallel to the axis of rotation) causes motion in the rotor. Axial flux motors typically have a high torque-to-weight ratio, which makes them ideal for transportation applications such as electric vehicles and even aviation.

Printed Circuit Board Stator
The key to the small size and light weight of Infinitum’s axial flux motors is the PCB stator. Infinitum’s air-core motors do not use iron cores or copper windings in the stator. Unlike conventional motors, the copper coils are etched directly into the PCB stator, resulting in a motor that is 50% less in weight and size than conventional designs. In electric vehicle powertrain applications, drive current from the traction inverter creates axial magnetic flux through the fixed PCB stator windings to move the rotor and drive the vehicle forward.
In addition to size and weight, other benefits of not having an iron core include reduced stator hysteresis and eddy current losses, resulting in higher efficiency or physical output per unit of power input.The PCB stator also improves motor reliability by eliminating potential points of failure associated with the copper windings and insulation found in conventional motors.
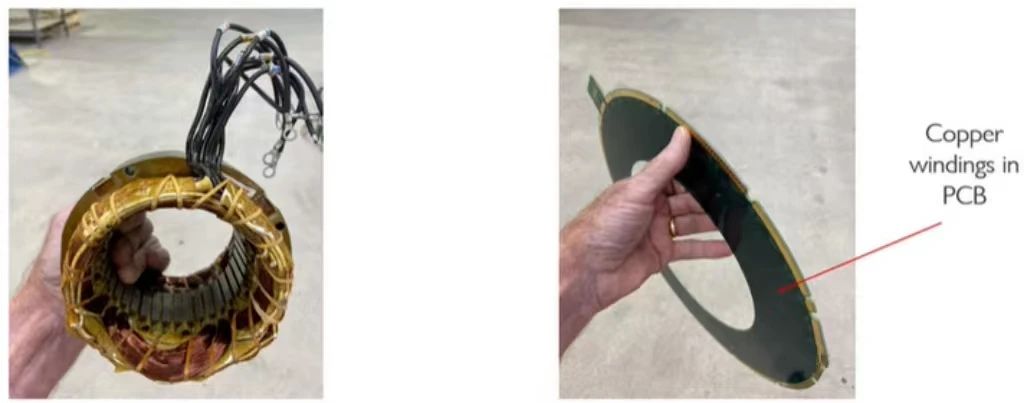
Modular design is scalable
Aircore Mobility utilizes a modular design that can be scaled to meet the power needs of an application without changing the core motor structure. With this approach, multiple PCB stators and rotors can be combined as needed to meet the power needs of applications ranging from small passenger cars to Class 8 commercial trucks such as the Tesla Semi. The flexibility of the design allows engineers to experiment with different configurations, quickly adding stators and rotors to determine which configuration best suits their power and torque requirements.
According to Ramon Guiart, Infinitum’s vice president of engineering, this higher power scalability compared to previous models is a key differentiator for Aircore Mobility, Guiart said, “The difference is in the scalability that we were able to achieve. These particular units are about 150 kW or 200 hp.” On the cost side, PCB stators can be manufactured using widely available standard circuit board production techniques.
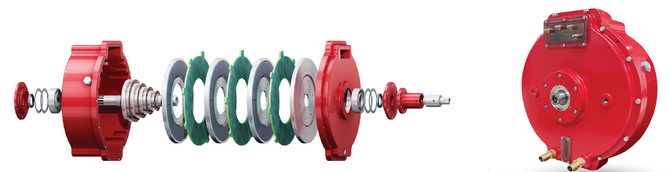
Cooling High Power Density Motors
The ability to add multiple rotors and stators allows Aircore motors to scale in power, but there are challenges in managing heat in the compact space of the motor. For Infinitum, replacing air cooling with an oil-based system was the answer to this challenge.
dJ Edrive products
Axial Flux Motors in Light Truck Range Extenders
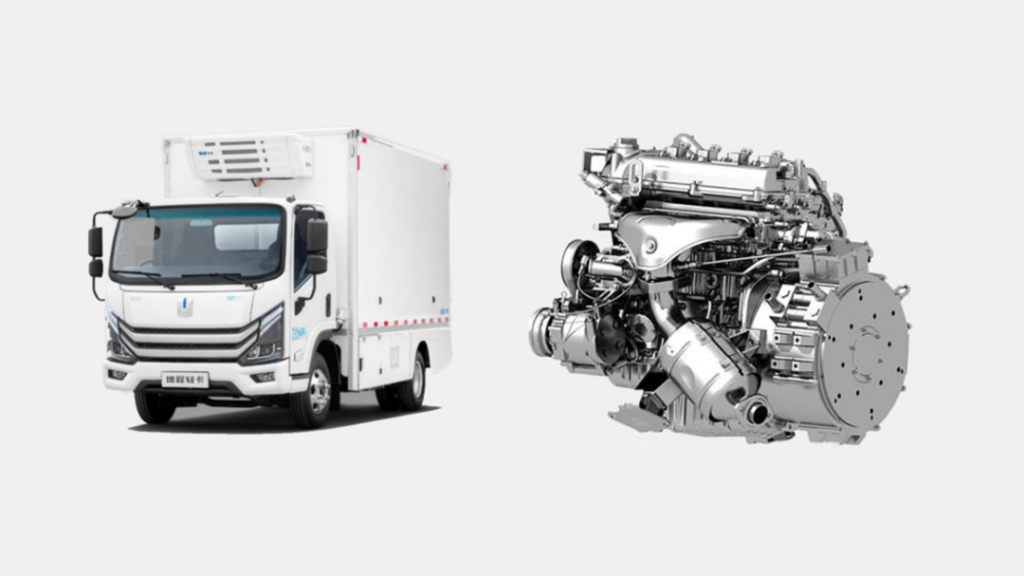
Double stator axial flux motor technology
The product adopts dual-stator axial flux motor technology, which reduces the volume by 1/3 and the weight by 30% compared with the mainstream products in the market. Its flat structure and low-speed, high-torque performance characteristics perfectly match the needs of range extender products for generators. The motor is not even beyond the engine’s air intake system after installation. The structural design of the complete range extender system is very compact, which can better adapt to the narrow space of the whole vehicle assembly and meet the demand of vehicle lightweight.

Carbon Fiber Wound Rotor Discs
The disc rotor of the product adopts the industry-leading carbon fiber winding process, which greatly reduces the risk of failure and has high reliability; in addition, the traditional paint dipping process is canceled, and a more advanced vacuum potting process is adopted, which ensures a clean and environmentally friendly production process and greatly improves the structural strength, and improves the NVH performance significantly; on the other hand, the product adopts the end-face waterway heat dissipation method independently researched and developed, which has an excellent cooling effect and significantly reduces the adverse effects of engine heat conduction on the motor, and the performance is very stable. On the other hand, the product adopts self-developed end face waterway heat dissipation method, which has excellent heat dissipation effect and significantly reduces the adverse effect of engine heat conduction to the motor, and the performance is very stable.
Stator Assembly
Stator Core Punching and Rolling Molding Process The stator core of the product adopts one-time molding process of punching and coiling, which has a very high material utilization rate and reduces the raw material cost by 30% compared with that of punching core; and the axial permanent magnet disk motor, with its unique magnetic flux structure, determines that its axial thickness is thinner than that of conventional motors by more than 2/3. The rotor disk is similar in structure to the flywheel and is axially mounted, which can replace the flywheel part of the range extender, not only reducing the manufacturing cost to a larger extent in the design and development of the range extender, but also improving the energy conversion efficiency.
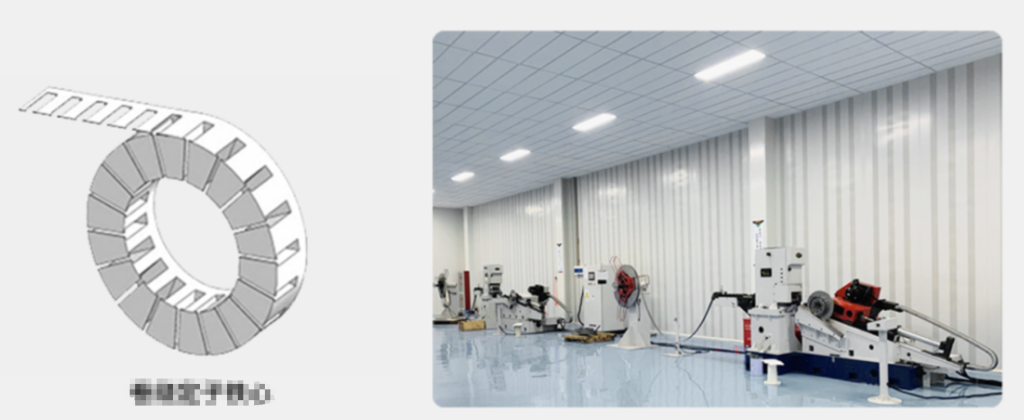
Core Punch Coil Molding Process
In terms of the efficiency of the range extender’s power generation, the product uses an axial flux permanent magnet motor to match the engine’s optimal fuel consumption point, which will make the system more efficient. Under the working condition where the rated speed of the gasoline and diesel engine is only from 1500rpm to 3000rpm, the axial flux permanent magnet motor is highly efficient and has a wide high efficiency range. The combined efficiency of the range extender system can reach more than 95%. The direct benefit of the efficient power generation system is a fuel saving of more than 20% for the vehicle.
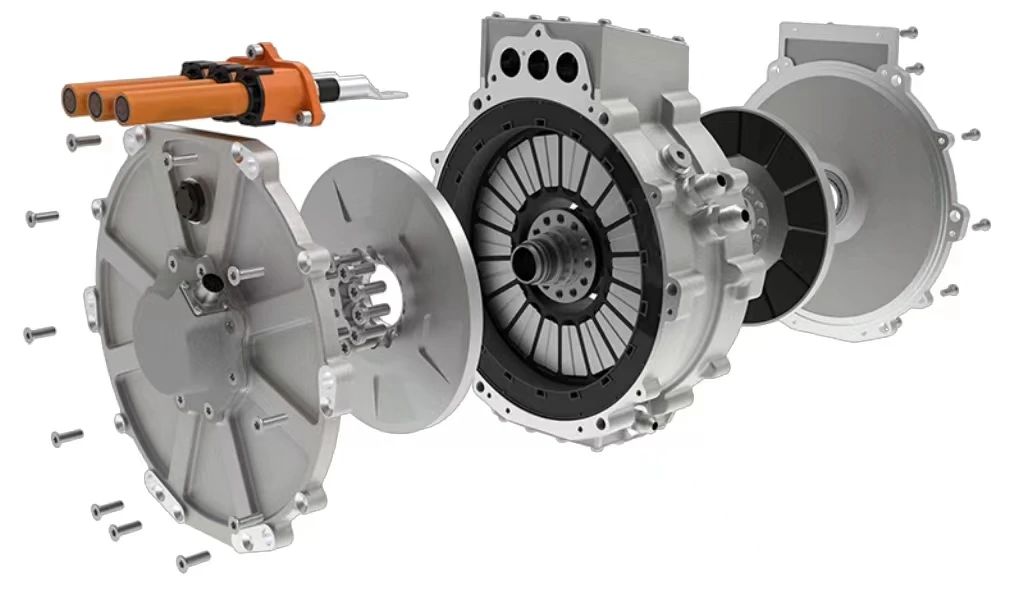