Motor shaft hollowing technology
Motor shaft hollowing, heat dissipation performance is good, and can prompt the motor lightweight.
Previously, the motor shaft is mostly solid, but due to the use of the motor shaft in the process of stress is often concentrated in the surface of the shaft, the core is subjected to less stress, according to the bending and torsion characteristics of the mechanics of the material, the motor shaft is properly hollowed out internally, and the external only need to increase the outer diameter of a very small amount of the hollow shaft to meet the same performance and utility and solid shaft, but the weight can be reduced significantly. At the same time, due to the hollowing out of the motor shaft, the cooling oil can enter the motor shaft, increasing the heat dissipation area and improving the heat dissipation efficiency. In the current trend of 800V high-voltage fast charging, the advantages of hollowing out the motor shaft are even greater. The current hollow motor shaft production method mainly has a solid shaft hollowing, welding, one-piece molding three ways, of which the welded and one-piece molding type in the production of more applications.
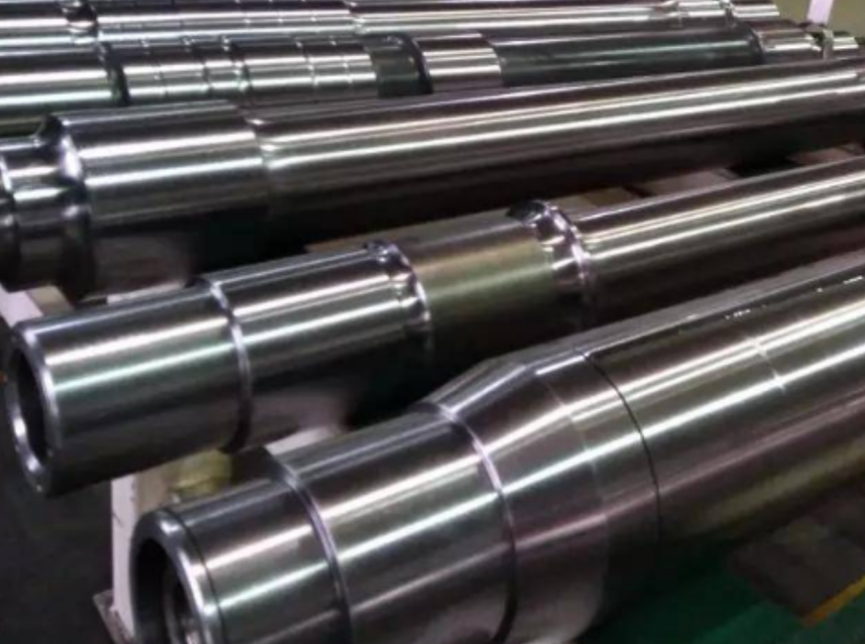
Welded hollow shafts, mainly through the use of extrusion molding to achieve the shaft step-type bore, and then by machining butt welding molding.
Through extrusion molding, the maximum possible to retain the shape of the bore with the product structure and strength requirements of the shape changes, the general product basic wall thickness can be designed in the following 5mm. Welding equipment is generally used butt friction welding or laser welding, such as butt friction welding, the butt joint position is generally about 3mm welding bulge. With laser welding, the welding depth is generally 3.5-4.5mm, and the welding strength can be guaranteed to be greater than 80% of the base material, and some suppliers can even achieve more than 90% of the base material strength through the use of stringent process control means. After the hollow shaft is welded, ultrasonic or X-ray inspection of the organization of the welded area and the quality of the weld is required to ensure product consistency.
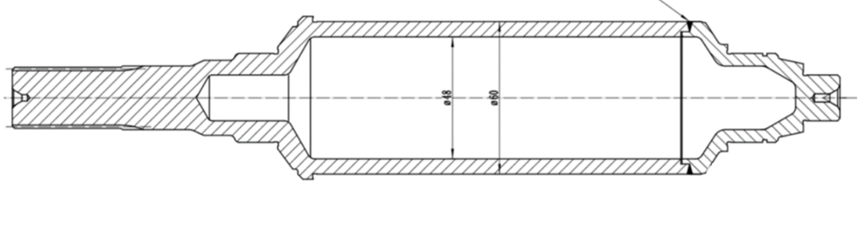
One-piece molding hollow shaft, mainly through the external equipment on the blank directly forging, so that the internal directly realize the shaft step type bore.
At present, the main use of radial forging molding and rotary forging molding, equipment are mainly imported, radial forging molding to FELLS company equipment is more typical, rotary forging to GFM company equipment as a typical representative. Radial forging, generally more than 4 symmetrical hammer in more than 240 times per minute under the high-frequency hammering, to achieve a small deformation of the billet directly hollow billet molding. Rotary forging molding, is in the billet circumferential direction uniformly arranged multiple hammer head, hammer head in the radial high-frequency forging workpiece at the same time around the axis of rotation, so that the billet cross-sectional size reduction, axial extension, so as to obtain the workpiece. Compared to traditional solid shafts, the manufacturing cost of integrally molded hollow shafts will go up by about 20%, but the motor shaft will generally lose 30-35% of its weight.