What is bearing galvanic corrosion?
When a motor is in operation, the potential difference generated between the ends of the rotating shaft or between the shaft and the shaft is called the shaft voltage. If the two ends of the shaft form a circuit through the motor seat, etc., the shaft current is generated under the action of the shaft voltage.
Shaft current is the shaft voltage through the motor, bearing, stator seat or auxiliary devices constitute a closed loop, because under normal circumstances, the shaft voltage is low, bearing lubricating oil film can play an insulating role in stifling the generation of shaft current; but when the shaft voltage is high, or the motor start-up instant oil film is not stable when the formation of the shaft, the shaft voltage will make the lubricating oil film discharge breakthrough to form a pathway to generate the shaft current.
Shaft current partial discharge energy release generated by the high temperature, can melt the bearing inner ring, outer ring or ball on the many tiny areas, and the formation of grooves, resulting in noise, vibration, if not found in time to deal with the bearing will lead to failure, a great impact on production.
Frequency control system in the high-frequency shaft current on the bearings of the most significant feature of galvanic corrosion in the motor bearing inner and outer rings, ball on the “rolling board” type dense groove stripes. What are the ways to fundamentally eliminate the motor shaft current? One is to increase the current relief device, that is, the addition of bypass brushes, the shaft current around the bearings to drain off; the second is the use of insulated bearings, blocking the path of the shaft current through the bearings, in order to block the path of the shaft current, at least one end of the motor to use electrically insulated bearings.
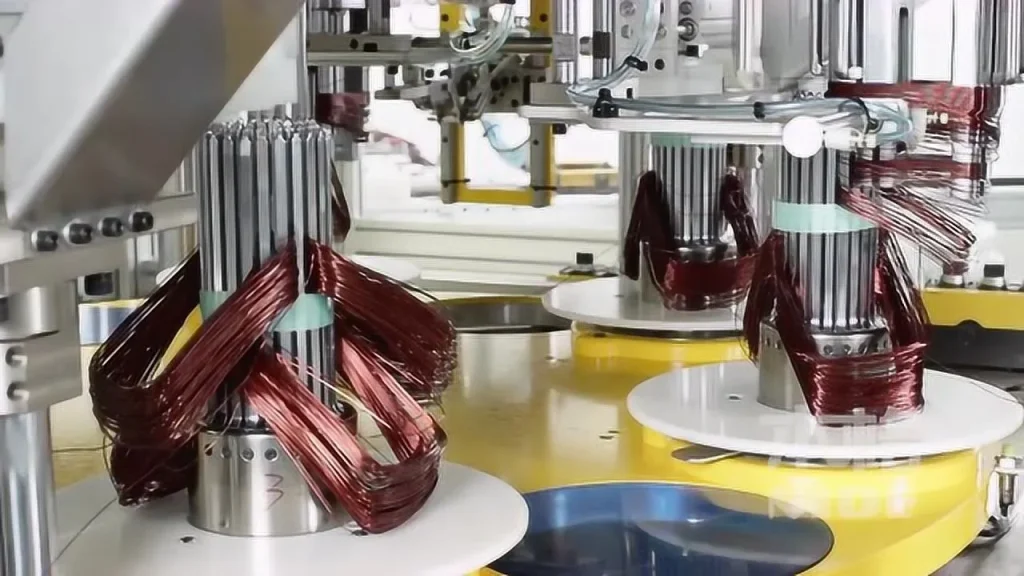
Overcurrents often occur in wheelset bearings and traction motors (railcars), DC and AC motors (power transmission systems) and generators (wind power). Overcurrents can cause damage to raceways and rolling elements as well as deterioration of the lubricant, which can lead to premature failure of the motor or generator, resulting in increased maintenance costs and losses such as production downtime. Rolling bearings used in electric motors, generators and other related equipment may be affected by the passage of electric current in the process of use, which will not only cause damage to the rolling elements and raceways in the bearings, but also affect the performance of the lubricant.
Bearing damage caused by current leakage will affect the motor vibration abnormality and increased noise. The motor cannot work normally.
Generally it is very difficult to completely eliminate the potential difference inside the bearing, but being able to stop or greatly reduce the current through the bearing will prevent galvanic corrosion from occurring in the bearing. The induced voltage generated along the shaft creates a current loop that passes through the bearing housing at the same time.
One reason for shaft voltage generation is due to the uneven distribution of magnetic flux within the motor, especially in some motors with a small number of pole pairs. In this case, the current loop can be completely cut off by insulating one end of the bearing, usually insulating the non-drive end bearing. If the voltage occurs between the shaft and the housing, the current will pass through each bearing in the same direction, in which case the bearings at both ends of the motor should be insulated.
The determining factor in selecting insulation is the time characteristic of the current. In the case of DC or low-frequency AC voltages, the effectiveness of the insulation depends on the pure resistance value of the insulation; in the case of high-frequency AC voltages (common in equipment using frequency converters), it depends on the capacitive resistance value of the insulation.
The best solution to these problems is the use of electrically insulated bearings. Bearings with a ceramic coating on either the inner or outer ring are called insulated bearings. The ceramic coating prevents the passage of electric current and has the ability to insulate. Hybrid bearings, in which the rolling elements are made of ceramic, also have an insulating capacity as the rolling elements prevent the passage of electric current.