Introduction to Precision Positioning Methods and Classification of Servo Motors
Servo motors mainly rely on the pulse to position, basically can be understood in this way, the servo motor receives 1 pulse, it will rotate 1 pulse corresponding to the angle, so as to realize the displacement, because the servo motor itself has the function of sending out pulses, so the servo motor will send out the corresponding number of pulses for every angle of rotation, so that and the servo motor receives the pulse to form the echo, or called closed loop, so that the system will be in this way, the system will know how many pulses are sent to the servo motor, and at the same time, how many pulses are received back, in this way, it can control the rotation of the motor very accurately, so as to realize accurate positioning, which can reach 0.001mm.
DC servo motors are divided into brushed and brushless motors. Brushed motor has low cost, simple structure, large starting torque, wide speed range, easy to control, requires maintenance, but maintenance is inconvenient (change carbon brushes), generates electromagnetic interference, and has environmental requirements. Therefore it can be used in common industrial and civil occasions which are sensitive to cost. Brushless motor is small in size, light in weight, large in output, fast in response, high in speed, small in inertia, smooth in rotation and stable in torque. The control is complex and easy to realize intelligentization, and its electronic phase change mode is flexible, which can be square wave phase change or sine wave phase change. The motor is maintenance-free, high efficiency, low operating temperature, very small electromagnetic radiation, long life, and can be used in a variety of environments.
AC servo motors are also brushless motors, divided into synchronous and asynchronous motors, at present, synchronous motors are generally used in motion control, which have a large power range and can achieve a great deal of power. Large inertia, the maximum rotation speed is low and decreases rapidly as the power increases. Thus it is suitable for low speed and smooth running applications.
The rotor inside the servo motor is a permanent magnet. The U/V/W three-phase electricity controlled by the servo driver forms an electromagnetic field, and the rotor rotates under this magnetic field, while the encoder that comes with the motor feeds back signals to the driver, which adjusts the angle of rotation of the rotor based on the comparison between the feedback value and the target value. The precision of the servo motor is determined by the precision (number of lines) of the encoder.
Difference between AC servo motor and brushless DC servo motor in function: AC servo is better because it is sinusoidal wave control, torque pulsation is small. DC servo is trapezoidal wave. But DC servo is simpler and cheaper.
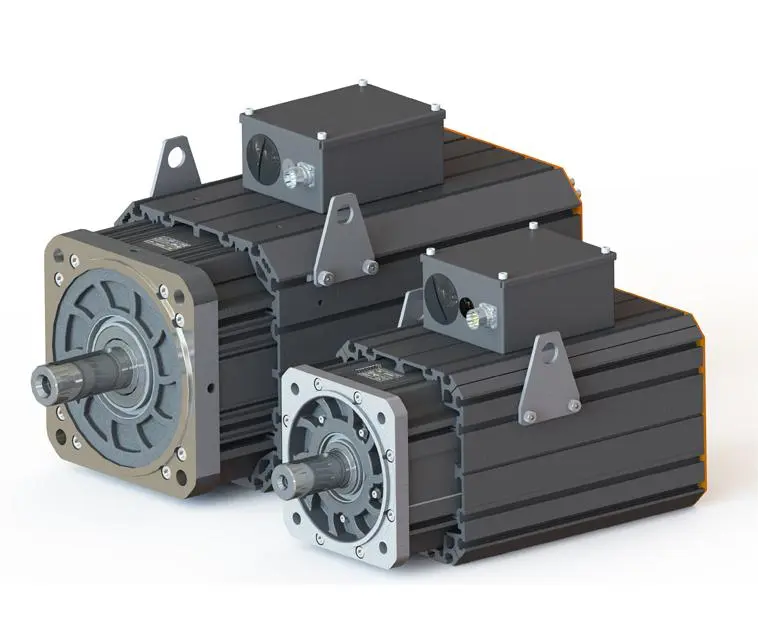
The weak magnetism function can also be used for fault detection and protection in some cases. For example, if a motor’s magnetic field abnormality or magnetoresistance abnormality is detected during motor operation, the system can apply weak magnetism to diagnose and troubleshoot the fault and protect the safe operation of the motor and equipment. In some special cases, the weak magnet function of the motor can also be used for specific application requirements, such as:
- Reducing the starting current shock: In some cases where it is necessary to limit the current shock of the power grid, by applying weak magnetism, it is possible to reduce the current shock of the motor during startup, reduce the impact on the power grid and equipment, and protect the stability of the electrical system.
- Reduced starting torque: For applications that require minimizing torque impact during startup, such as scenarios that require less mechanical impact during startup, the weak magnet function can achieve a gradual increase in torque, smooth startup, and protection of the mechanical drive system.
- Reducing start-up power demand: The weak magnet function can help reduce the power demand during motor start-up, especially for high-power motors or in cases where power supply conditions are limited, reducing the impact on the power grid and electrical equipment, and improving the energy efficiency of the system.
- Prevent overload protection triggering: In some cases, the motor may be subject to overload protection during startup. By applying weak magnetism, the load on the motor during startup can be reduced to avoid triggering of overload protection and protect the safe operation of the motor and the system.
In general, the weak magnetic function of the motor plays an important role in the motor starting process in terms of smooth starting, protection of equipment, energy saving and so on. By reasonably applying the weak magnetic function, the stability, reliability and safety of the motor system can be improved to meet the needs of different application scenarios.