Servomotors working principle
People want to use the “servo mechanism” as a handy taming tool, obeying the requirements of the control signal and action. Before the signal comes, the rotor is stationary; after the signal comes, the rotor turns immediately; when the signal disappears, the rotor can stop itself instantly. Because of its “servo” performance, hence the name.
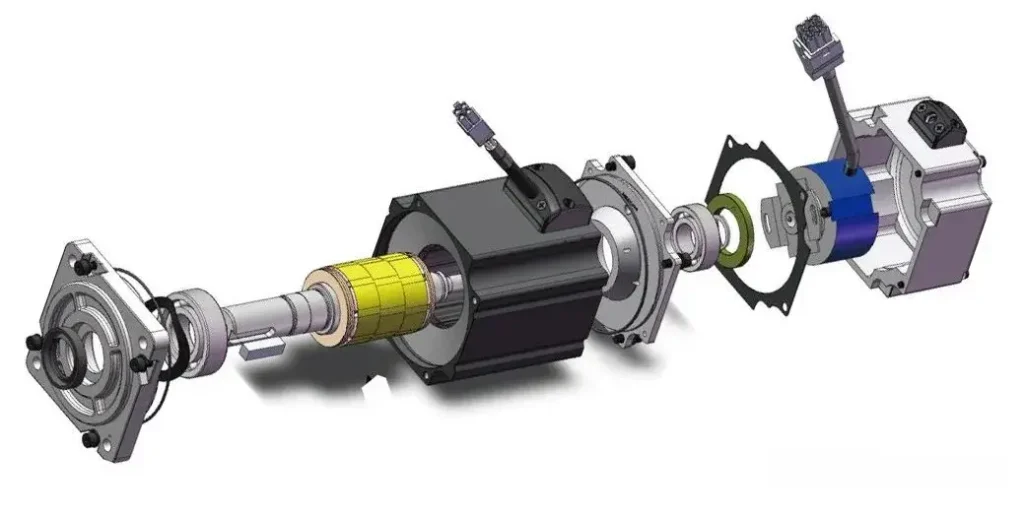
Servo system: It is an automatic control system that enables the output controlled quantities such as position, orientation and state of an object to follow the arbitrary change of the input target (or given value). Servo’s main task is according to the requirements of the control command, the power amplification, transformation and regulation and other processing, so that the output torque, speed and position control of the drive device is very flexible and convenient.
Servo system: It is an automatic control system that enables the output controlled quantities such as position, orientation and state of an object to follow the arbitrary change of the input target (or given value). Servo’s main task is according to the requirements of the control command, the power amplification, transformation and regulation and other processing, so that the output torque, speed and position control of the drive device is very flexible and convenient.
Servomotors Working Principle
Servomotor, also known as an executive motor, is used as an executive element in an automatic control system to convert the received electrical signal into an angular displacement or angular velocity output on the motor shaft. Its main feature is that there is no self-rotation when the signal voltage is zero, and the rotational speed decreases uniformly with the increase of torque.
Servo motor is a typical closed-loop feedback system, the reduction gear set driven by the motor, its terminal (output) drives a linear proportional potentiometer for position detection, the potentiometer will be converted into a proportional voltage to the control circuit board, the control circuit board will be compared with the input control pulse signal to generate a corrective pulse, and drive the motor to rotate in the forward or reverse direction, so that the gear set of the output position with the desired value, so that the corrective pulse tends to 0, so as to achieve the servo motor accurate positioning purposes.
The rotor inside the servo motor is a permanent magnet. The U/V/W three-phase electricity controlled by the driver forms an electromagnetic field, and the rotor rotates under the action of this magnetic field, while the encoder that comes with the motor feeds back signals to the driver, who adjusts the angle of rotation of the rotor based on the comparison between the feedback value and the target value. The precision of the servo motor is determined by the precision (number of lines) of the encoder.
AC Servomotors
AC servo motor stator structure is basically similar to capacitor split-phase single-phase asynchronous motor. The stator is equipped with two windings with 90° difference in position, one is the excitation winding Rf, which is always connected to the AC voltage Uf; the other is the control winding L, connected to the control signal voltage Uc. So the AC servo motor is also known as two servo motors.
AC servo motor rotor is usually made into a squirrel cage, but in order to make the servo motor has a wide speed range, linear mechanical characteristics, no “spin” phenomenon and fast response performance, it is compared with ordinary motors, should have a large rotor resistance and small inertia of the two characteristics. Currently more widely used rotor structure has two forms: one is made of high-resistivity conductive materials made of high resistivity guide strip of the squirrel cage rotor, in order to reduce the rotor’s inertia, the rotor to do a long and thin; the other is made of aluminum alloy hollow cup shaped rotor, the cup wall is very thin, only 0.2-0.3mm, in order to reduce the magnetic resistance of the magnetic circuit to be placed in the hollow cup shaped rotor within the fixed inner stator. The hollow cup rotor has a very small moment of inertia, quick response, and smooth operation, so it is widely used.
When there is no control voltage, there is only a pulsating magnetic field generated by the excitation winding in the stator, and the rotor is stationary. When there is a control voltage, a rotating magnetic field is generated in the stator, and the rotor rotates in the direction of the rotating magnetic field. In the case of a constant load, the rotational speed of the motor varies with the magnitude of the control voltage, and the servomotor will be inverted when the phase of the control voltage is reversed.
The working principle of AC servo motor and split-phase single-phase asynchronous motor is similar, but the rotor resistance of the former is much larger than the latter, so the servo motor has three significant features compared with the single-phase asynchronous motor:
1. Starting torque
Due to the large rotor resistance, its torque characteristic curve as shown in curve 1 in Figure 3, compared with the ordinary asynchronous motor’s torque characteristic curve 2, there is a significant difference. It can make the critical torque rate S0>1, which not only makes the torque characteristic (mechanical characteristic) closer to linear, but also has a large starting torque. Therefore, when the stator has a control voltage, the rotor rotates immediately, that is, it has the characteristics of fast starting and high sensitivity.
2. Wide operation range
3. No self-rotation phenomenon
Normal operation of the servo motor, as long as the loss of control voltage, the motor immediately stops running. When the servo motor loses the control voltage, it is in single-phase operation state, due to the rotor resistance, the two rotating magnetic fields rotating in opposite directions in the stator and the rotor action produced by the two torque characteristics (T1-S1, T2-S2 curves) as well as the synthetic torque characteristics (T-S curve).
The output power of AC servo motor is generally 0.1-100 W. When the power supply frequency is 50Hz, the voltage is 36V, 110V, 220, 380V; when the power supply frequency is 400Hz, the voltage is 20V, 26V, 36V, 115V and so on.
Summarize
AC servo motor runs smoothly and has low noise. However, the control characteristic is nonlinear, and due to high rotor resistance, high loss and low efficiency, so compared with the same capacity DC servo motor, it is large and heavy, so it is only suitable for 0.5-100W small power control system.